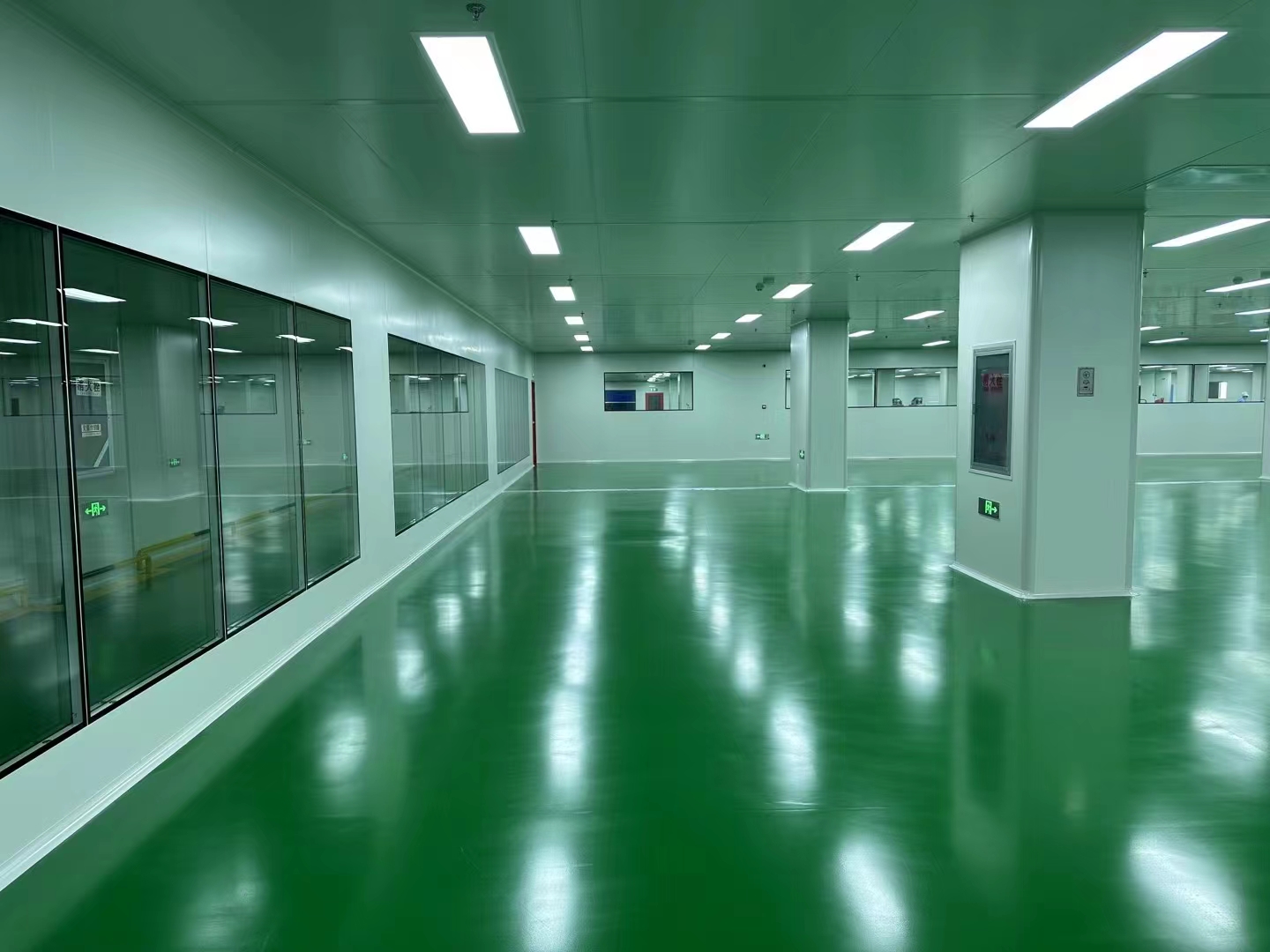
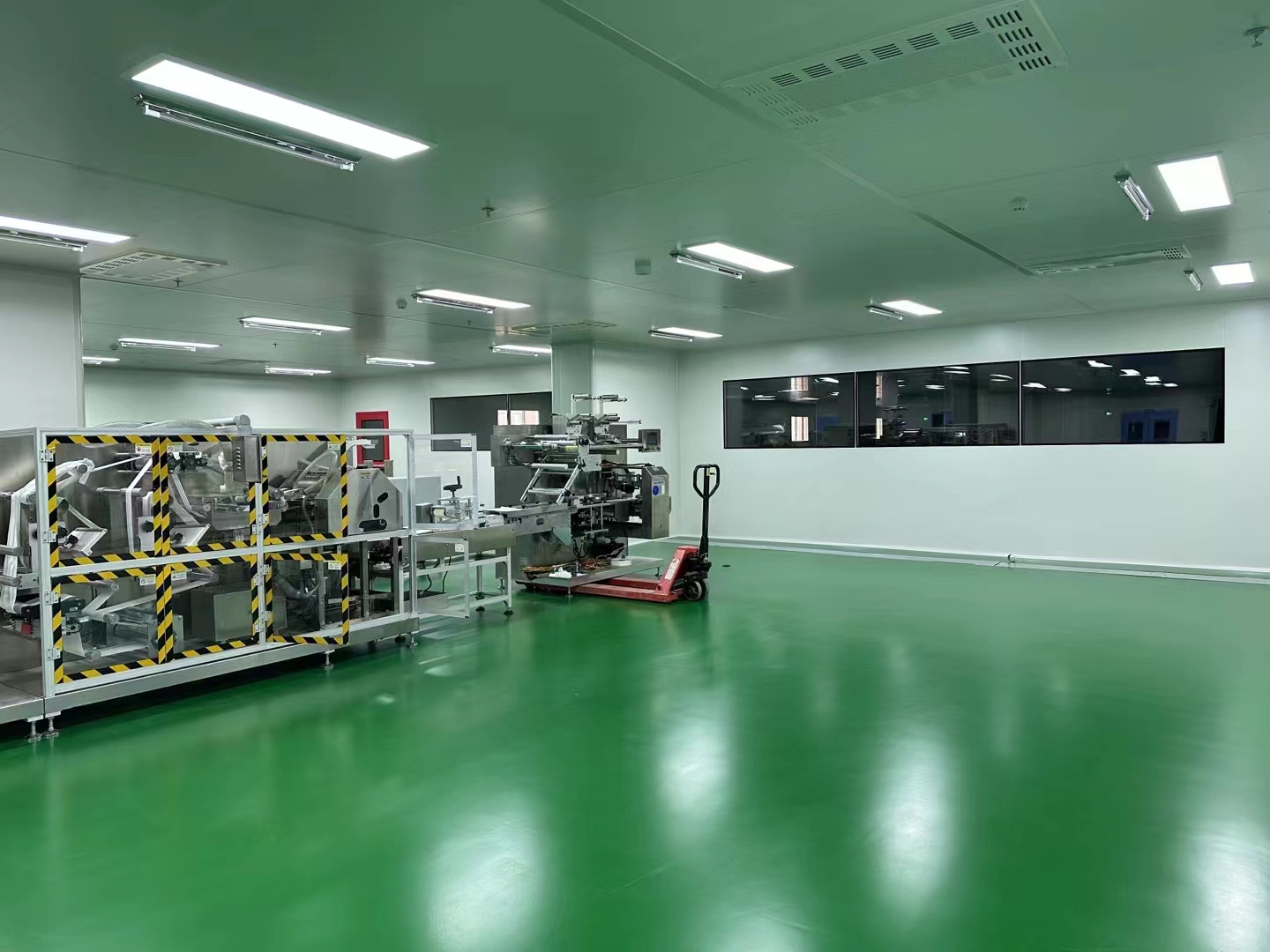
The fire system design in clean room must take into account the requirements of clean environment and fire safety regulations. Special attention should be paid to preventing pollution and avoiding airflow interference, while ensuring rapid and effective fire response.
1. Selection of fire systems
Gas fire systems
HFC-227ea: commonly used, non-conductive, residue-free, friendly to electronic equipment, but airtightness must be considered (dust-free clean rooms are usually well-sealed).
IG-541 (inert gas): environmentally friendly and non-toxic, but requires a larger storage space.
CO₂ system: use with caution, may be harmful to personnel, and is only suitable for unattended areas.
Applicable scenarios: electrical rooms, precision instrument areas, data centers and other areas that are afraid of water and pollution.
Automatic water spraying system
Pre-action sprinkler system: the pipeline is usually inflated with gas, and in case of fire, it is exhausted first and then filled with water to avoid accidental spraying and pollution (recommended for clean rooms).
Avoid using wet systems: the pipeline is filled with water for a long time, and the risk of leakage is high.
Nozzle selection: stainless steel material, dustproof and corrosion-resistant, sealed and protected after installation.
High-pressure water mist system
Water-saving and high fire extinguishing efficiency, can reduce smoke and dust locally, but the impact on cleanliness needs to be verified.
Fire extinguisher configuration
Portable: CO₂ or dry powder fire extinguisher (placed in air lock room or corridor to avoid direct entry into clean area).
Embedded fire extinguisher box: reduce protruding structure to avoid dust accumulation.
2. Dust-free environment adaptation design
Pipeline and equipment sealing
Fire protection pipelines need to be sealed with epoxy resin or stainless steel sleeves at the wall to prevent particle leakage.
After installation, sprinklers, smoke sensors, etc. need to be temporarily protected with dust covers and removed before production.
Materials and surface treatment
Stainless steel or galvanized steel pipes are selected, with smooth and easy-to-clean surfaces to avoid dust.
Valves, boxes, etc. should be made of non-shedding and corrosion-resistant materials.
Airflow organization compatibility
The location of smoke detectors and nozzles should avoid hepa box to avoid interfering with airflow balance.
There should be an exhaust ventilation plan after the fire extinguishing agent is released to prevent gas stagnation.
3. Fire alarm system
Detector type
Aspirating smoke detector (ASD): It samples air through pipes, has high sensitivity, and is suitable for high airflow environments.
Point-type smoke/heat detector: It is necessary to select a special model for clean rooms, which is dust-proof and anti-static.
Flame detector: It is suitable for flammable liquid or gas areas (such as chemical storage rooms).
Alarm linkage
The fire signal should be linked to shut down the fresh air system (to prevent smoke diffusion), but the smoke exhaust function must be retained.
Before starting the fire extinguishing system, the fire damper must be automatically closed to ensure the fire extinguishing concentration.
4. Smoke exhaust and smoke prevention and exhaust design
Mechanical smoke exhaust system
The location of the smoke exhaust port should avoid the core area of the clean area to reduce pollution.
The smoke exhaust duct should be equipped with a fire damper (fused and closed at 70℃), and the outer wall insulation material should not produce dust.
Positive pressure control
When extinguishing a fire, turn off the air supply, but maintain a slight positive pressure in the buffer room to prevent external pollutants from invading.
5. Specifications and acceptance
Main standards
Chinese specifications: GB 50073 "Cleanroom Design Specifications", GB 50016 "Building Design Fire Protection Specifications", GB 50222 "Building Interior Decoration Fire Protection Specifications".
International references: NFPA 75 (Electronic Equipment Protection), ISO 14644 (Cleanroom Standard).
Acceptance points
Fire extinguishing agent concentration test (such as heptafluoropropane spray test).
Leak test (to ensure the sealing of pipelines/enclosure structures).
Linkage test (alarm, air conditioning cut-off, smoke exhaust start, etc.).
6. Precautions for special scenarios
Biological clean room: avoid using fire extinguishing agents that may corrode biological equipment (such as certain dry powders).
Electronic clean room: give priority to non-conductive fire extinguishing systems to prevent electrostatic damage.
Explosion-proof area: combined with explosion-proof electrical appliance design, select explosion-proof detectors.
Summary and suggestions
The fire protection in clean rooms requires "effective fire extinguishing + minimal pollution". Recommended combination:
Core equipment area: HFC-227ea gas fire extinguishing + aspirating smoke detection.
General area: pre-action sprinkler + point-type smoke detector.
Corridor/exit: fire extinguisher + mechanical smoke exhaust.
During the construction phase, close cooperation with HVAC and decoration professionals is required to ensure seamless connection between fire protection facilities and clean requirements.
Post time: Jul-16-2025