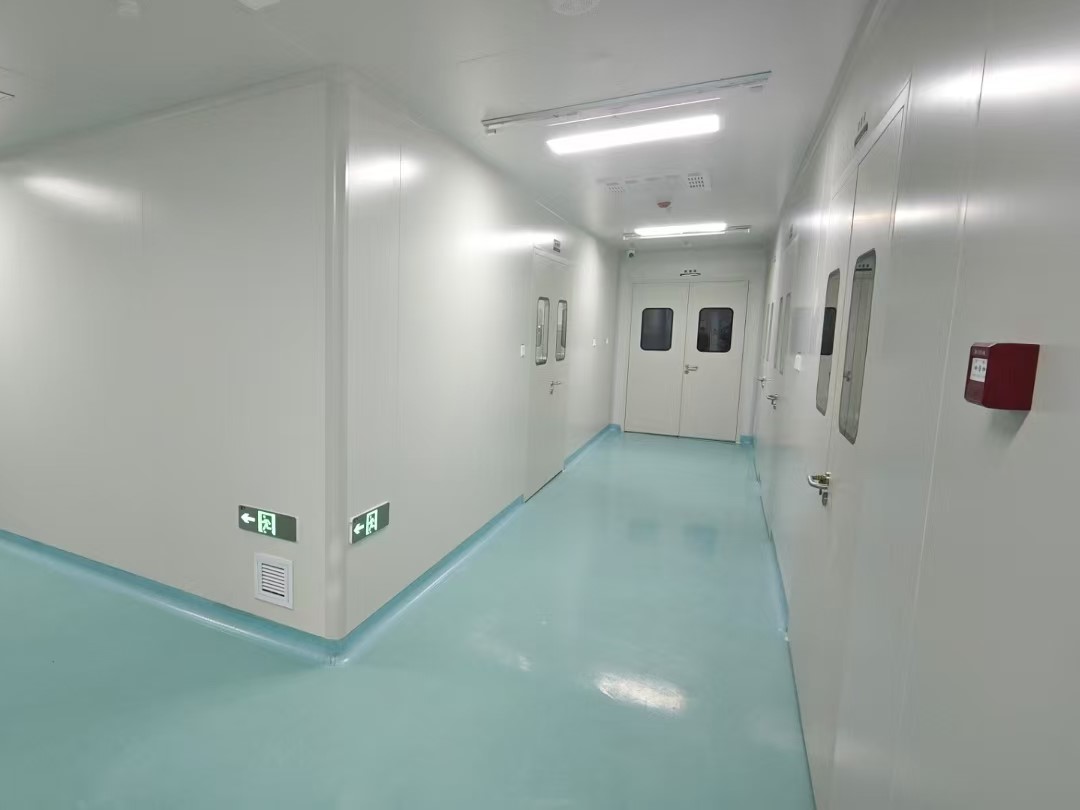
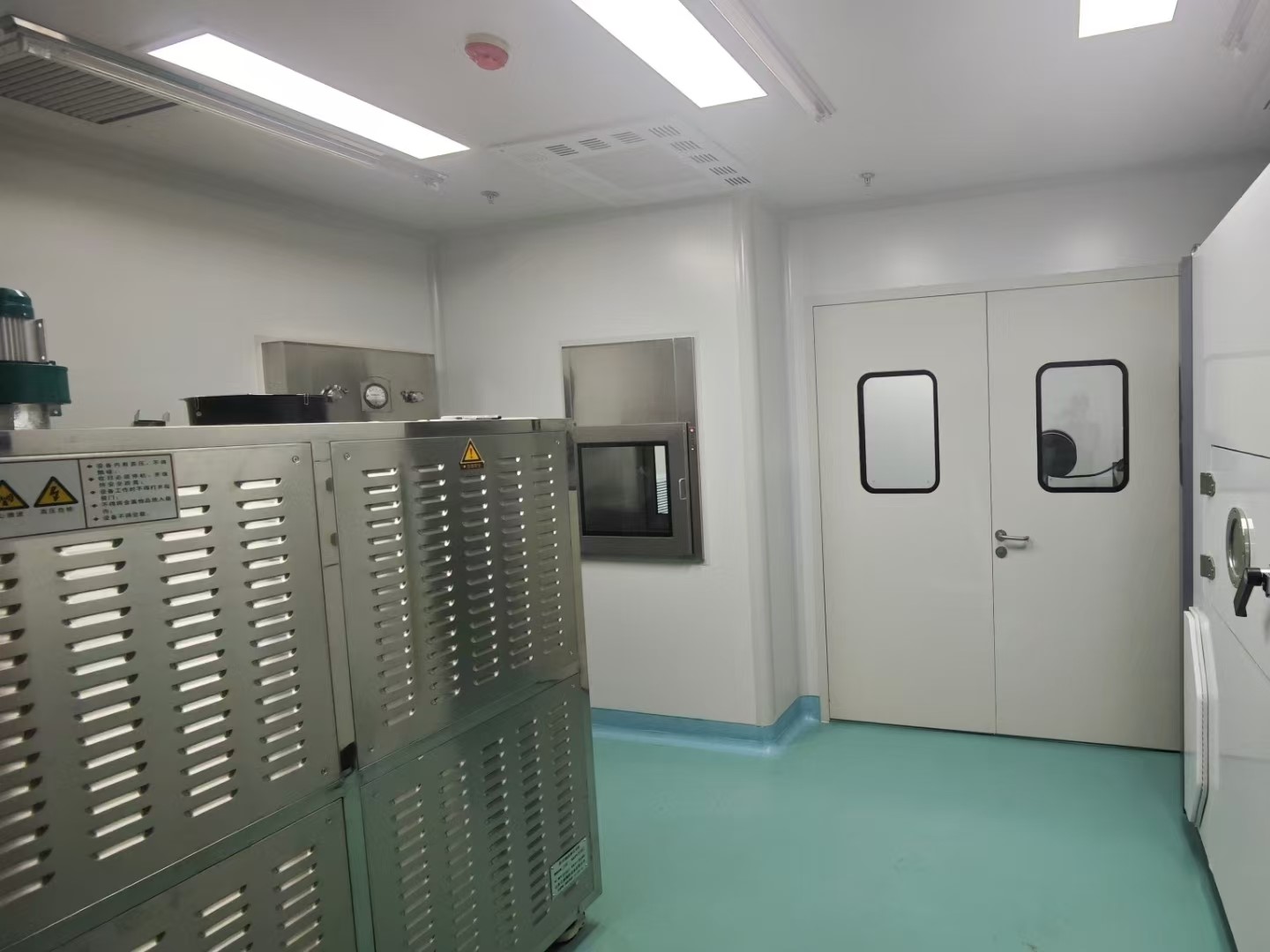
The decoration layout requirements of professional clean room must ensure that the environmental cleanliness, temperature and humidity, airflow organization, etc. meet the production requirements, as follows:
1. Plane layout
Functional zoning: Clearly divide the clean area, quasi-clean area and non-clean area to avoid cross-contamination.
Separation of human flow and logistics: Set up independent human flow and logistics channels to reduce the risk of cross-contamination.
Buffer zone setting: Set up a buffer room at the entrance of the clean area, equipped with an air shower or airlock room.
2. Walls, floors and ceilings
Walls: Use smooth, corrosion-resistant and easy-to-clean materials, such as steel sandwich panels, stainless steel sandwich panels, etc.
Floor: Use anti-static, wear-resistant and easy-to-clean materials, such as PVC floors, epoxy self-leveling, etc.
Ceiling: Use materials with good sealing and dust-resistant properties, such as sandwich panels, aluminum gussets, etc.
3. Air purification system
Hepa filter: Install a hepa filter (HEPA) or ultra-hepa filter (ULPA) at the air outlet to ensure air cleanliness.
Airflow organization: Use unidirectional or non-unidirectional flow to ensure uniform distribution of airflow and avoid dead corners.
Pressure difference control: Maintain appropriate pressure difference between areas of different clean levels to prevent pollution from spreading.
4. Temperature and humidity control
Temperature: According to process requirements, it is usually controlled at 20-24℃.
Humidity: Generally controlled at 45%-65%, and special processes need to be adjusted according to needs.
5. Lighting
Illumination: The illumination in clean area is generally not less than 300 lux, and special areas are adjusted as needed.
Lamps: Use clean lamps that are not easy to accumulate dust and easy to clean, and install them in an embedded manner.
6. Electrical system
Power distribution: The distribution box and sockets should be installed outside clean area, and the equipment that must enter clean area should be sealed.
Anti-static: The floor and work bench should have anti-static function to prevent the impact of static electricity on products and equipment.
7. Water supply and drainage system
Water supply: Use stainless steel pipes to avoid rust and pollution.
Drainage: The floor drain should have a water seal to prevent odor and pollutants from flowing back.
8. Fire protection system
Fire protection facilities: equipped with smoke sensors, temperature sensors, fire extinguishers, etc., in compliance with fire protection regulations.
Emergency passages: set up obvious emergency exits and evacuation passages.
9. Other requirements
Noise control: take noise reduction measures to ensure that the noise is less than 65 decibels.
Equipment selection: select easy-to-clean and dust-free equipment to avoid affecting the clean environment.
10. Verification and testing
Cleanliness test: regularly test the number of dust particles and microorganisms in the air.
Pressure difference test: regularly check the pressure difference of each area to ensure that the pressure difference meets the requirements.
In summary, the decoration layout of the clean room needs to comprehensively consider factors such as cleanliness, temperature and humidity, and airflow organization to ensure that it meets production process requirements. At the same time, regular testing and maintenance are required to ensure the stability of the clean room environment.
Post time: Jul-03-2025