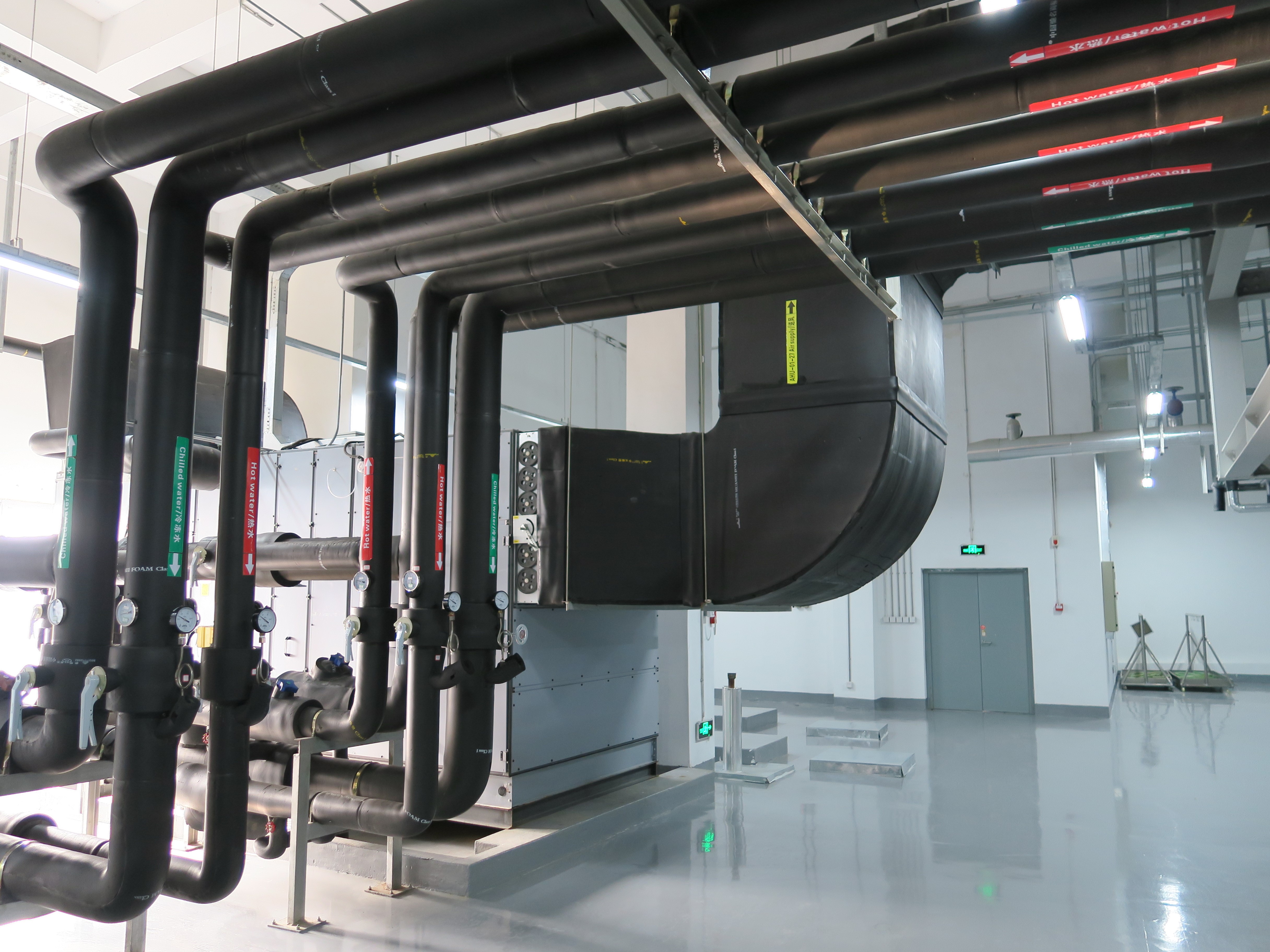
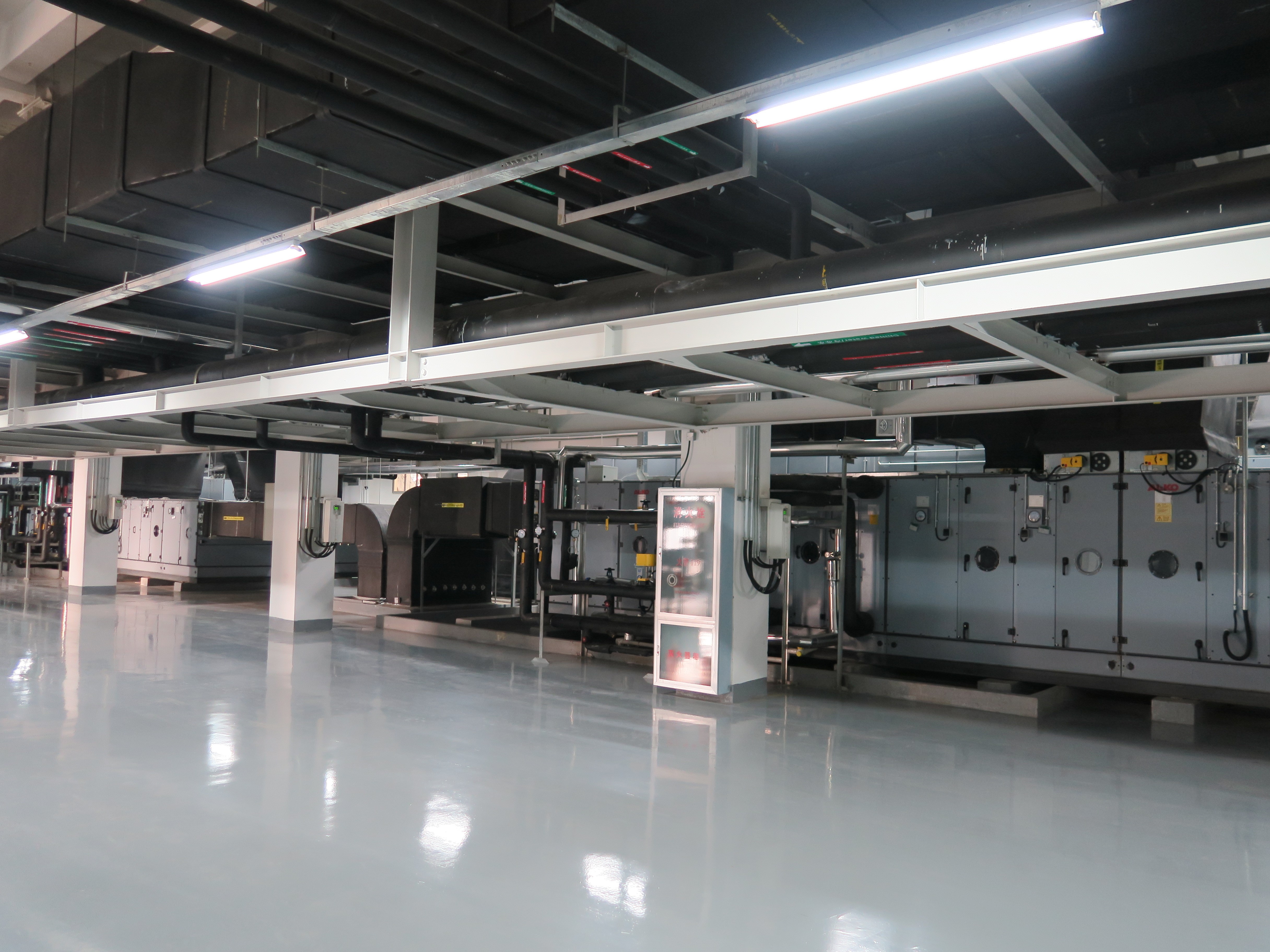
In the decoration of GMP pharmaceutical clean room, the HVAC system is the top priority. It can be said that whether the environmental control of the clean room can meet the requirements mainly depends on HVAC system. Heating ventilation and air conditioning (HVAC) system is also called purification air conditioning system in pharmaceutical GMP clean room. The HVAC system mainly processes air entering room and controls air temperature, humidity, suspended particles, microorganisms, pressure difference and other indicators of the pharmaceutical production environment to ensure that environmental parameters meet the requirements of pharmaceutical quality and avoid the occurrence of air pollution and cross-contamination while providing a comfortable environment for operators. In addition, pharmaceutical clean room HVAC systems can also reduce and prevent the adverse effects of drugs on people during production process, and protect the surrounding environment.
Overall design of air conditioning purification system
The overall unit of the air conditioning purification system and its components should be designed according to environmental requirements. The unit mainly includes functional sections such as heating, cooling, humidification, dehumidification, and filtration. Other components include exhaust fans, return air fans, heat energy recovery systems, etc. There should be no falling objects in internal structure of HVAC system, and the gaps should be as small as possible to prevent dust accumulation. HVAC systems must be easy to clean and withstand necessary fumigation and disinfection.
1. HVAC system type
Air conditioning purification systems can be divided into DC air conditioning systems and recirculation air conditioning systems. The DC air conditioning system sends the processed outdoor air that can meet the space requirements into room, and then discharges all the air. The system uses all outdoor fresh air. Recirculation air conditioning system, that is, clean room air supply is mixed with part of the treated outdoor fresh air and part of the return air from clean room space. Since recirculation air conditioning system has the advantages of low initial investment and low operating costs, the recirculation air conditioning system should be used as rationally as possible in design of the air conditioning system. The air in some special production areas cannot be recycled, such as clean room (area) where dust is emitted during production process, and cross-contamination cannot be avoided if the indoor air is treated; organic solvents are used in production, and gas accumulation may cause explosions or fires and dangerous processes; pathogen operation areas; radioactive pharmaceutical production areas; production processes that produce a large amount of harmful substances, odors or volatile gases during production process.
A pharmaceutical production area can usually be divided into several areas with different cleanliness levels. Different clean areas should be equipped with independent air handling units. Each air conditioning system is physically separated to prevent cross-contamination between products. Independent air handling units can also be used in different product areas or separate different areas to isolate harmful substances through strict air filtration and prevent cross-contamination through air duct system, such as production areas, auxiliary production areas, storage areas, administrative areas, etc. should be equipped with separate air handling unit. For production areas with different operating shifts or usage times and large differences in temperature and humidity control requirements, the air conditioning systems should also be set up separately.
2. Functions and measures
(1). Heating and cooling
The production environment should be adapted to the production requirements. When there are no special requirements for pharmaceutical production, the temperature range of Class C and Class D clean rooms can be controlled at 18~26°C, and the temperature range of Class A and Class B clean rooms can be controlled at 20~24°C. In clean room air conditioning system, hot and cold coils with heat transfer fins, tubular electric heating, etc. can be used to heat and cool the air, and treat air to the temperature required by clean room. When the fresh air volume is large, preheating of the fresh air should be considered to prevent the downstream coils from freezing. Or use hot and cold solvents, such as hot and cold water, saturated steam, ethylene glycol, various refrigerants, etc. When determining the hot and cold solvents, the requirements for air heating or cooling treatment, hygienic requirements, product quality, economics, etc. Make a choice based on cost and other conditions.
(2). Humidification and dehumidification
The relative humidity of the clean room should be compatible with the pharmaceutical production requirements, and the pharmaceutical production environment and operator comfort should be ensured. When there are no special requirements for pharmaceutical production, the relative humidity of Class C and Class D clean areas is controlled at 45% to 65%, and the relative humidity of Class A and Class B clean areas is controlled at 45% to 60%.
Sterile powdered products or most solid preparations require a low relative humidity production environment. Dehumidifiers and post-coolers can be considered for dehumidification. Due to higher investment and operating costs, the dew point temperature usually needs to be lower than 5°C. The production environment with higher humidity can be maintained by using factory steam, pure steam prepared from purified water, or through a steam humidifier. When clean room has relative humidity requirements, the outdoor air in summer should be cooled by the cooler and then thermally heated by the heater to adjust the relative humidity. If indoor static electricity needs to be controlled, humidification should be considered in cold or dry climates.
(3). Filter
The number of dust particles and microorganisms in fresh air and return air can be reduced to a minimum through filters in HVAC system, allowing the production area to meet normal cleanliness requirements. In air-conditioning purification systems, air filtration is generally divided into three stages: pre-filtration, intermediate filtration and hepa filtration. Each stage uses filters of different materials. The prefilter is the lowest and is installed at the beginning of the air handling unit. It can capture larger particles in the air (particle size above 3 microns). The intermediate filtration is located downstream of the pre-filter and is installed in the middle of the air handling unit where the return air enters. It is used to capture smaller particles (particle size above 0.3 microns). The final filtration is located in discharge section of air handling unit, which can keep the pipeline clean and extend the service life of the terminal filter.
When clean room cleanliness level is high, a hepa filter is installed downstream of the final filtration as a terminal filtration device. The terminal filter device is located at the end of the air handle unit and is installed on the ceiling or wall of the room. It can ensure the supply of the cleanest air and is used to dilute or send out the particles released in clean room, such as Class B clean room or Class A in Class B clean room background.
(4).Pressure control
Most clean room maintain a positive pressure, while the anteroom leading to this clean room maintains successively lower and lower positive pressures, up to a zero baseline level for uncontrolled spaces (general buildings). The pressure difference between clean areas and non-clean areas and between clean areas of different levels should not be less than 10 Pa. When necessary, appropriate pressure gradients should also be maintained between different functional areas (operating rooms) of the same cleanliness level. The positive pressure maintained in clean room can be achieved by air supply volume being bigger than air exhaust volume. Changing air supply volume can adjust pressure difference between each room. Special drug production, such as penicillin drugs, operating areas that produce large amounts of dust should maintain a relatively negative pressure.
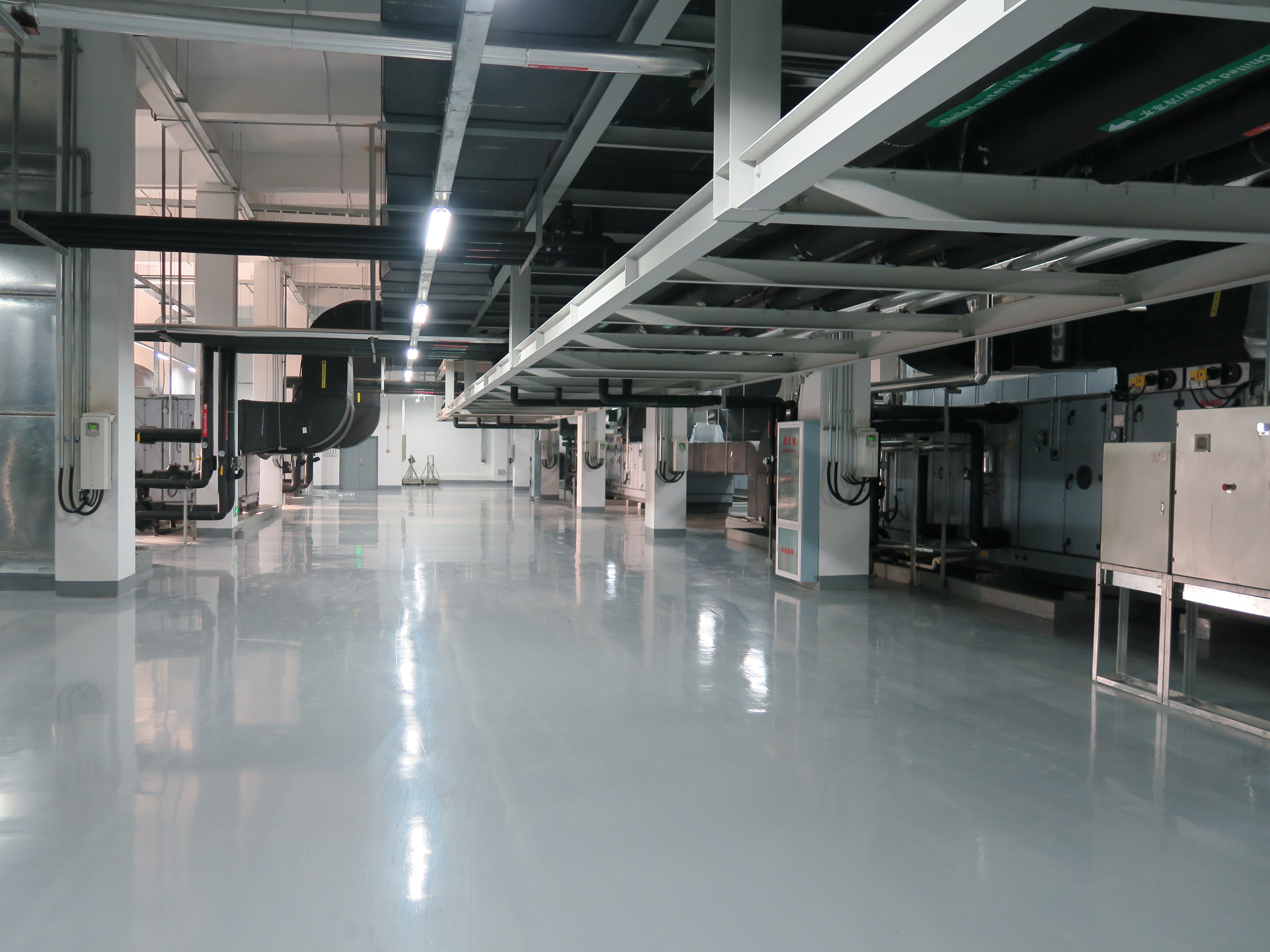
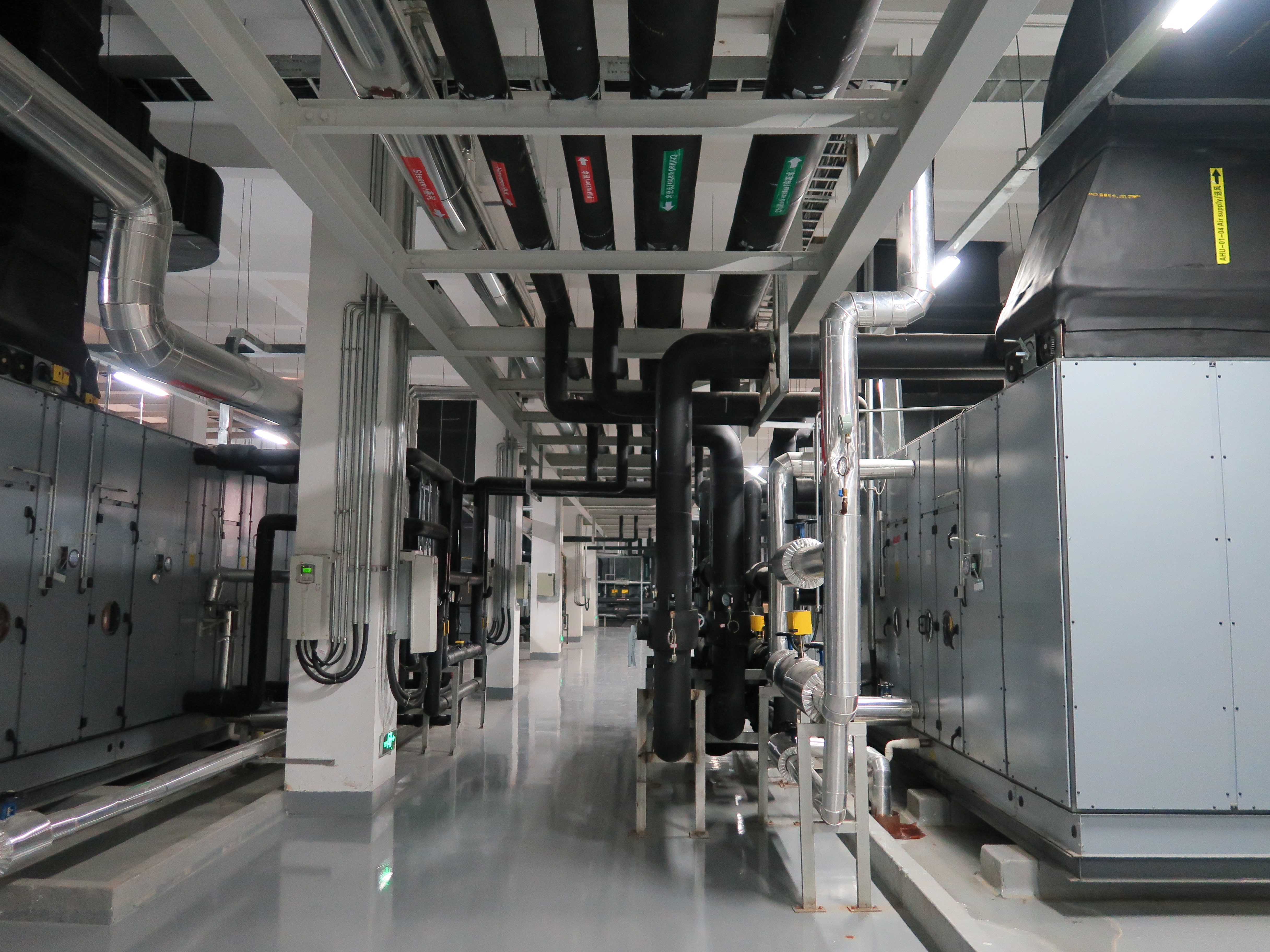
Post time: Dec-19-2023