The main function of the clean workshop cleanroom project is to control the air cleanliness and temperature and humidity in which products (such as silicon chips, etc) can get contact, so that products can be manufactured in a good environmental space, which we call clean workshop cleanroom project.
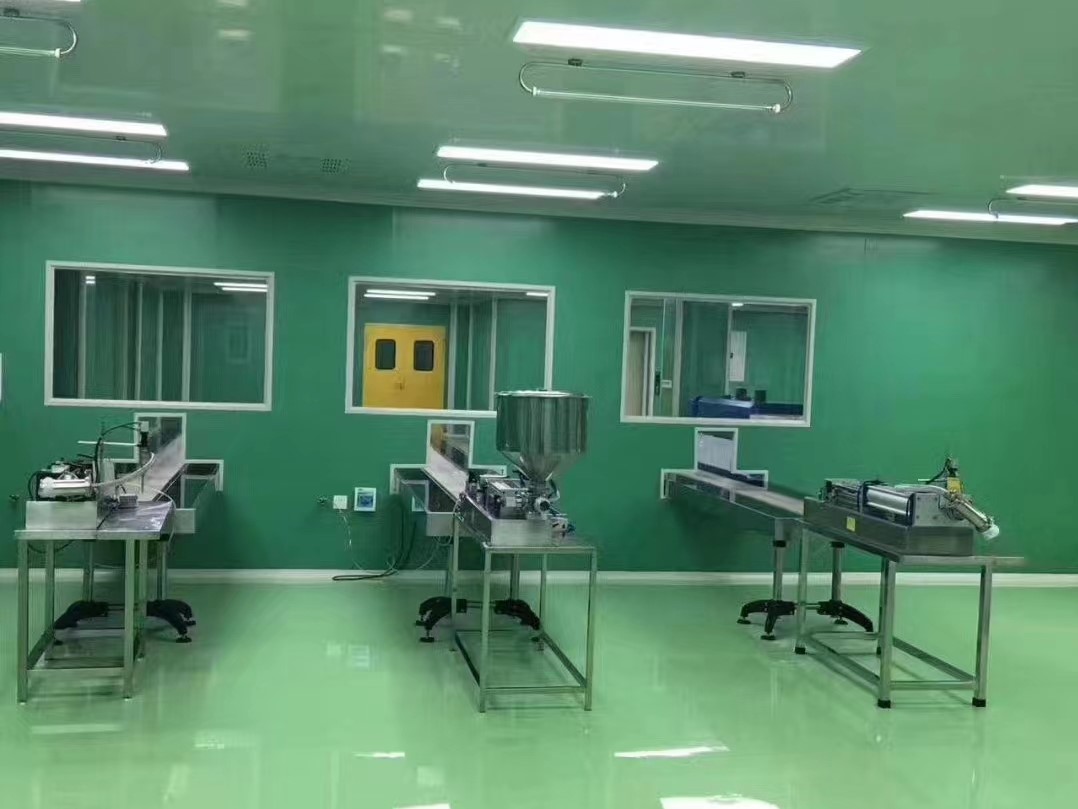
Clean workshop cleanroom project can be divided into three types. According to international practice, the cleanliness level of dust free cleanroom is mainly based on the number of particles per cubic meter in air with a diameter bigger than the distinguishing standard. That is to say, the so-called dust free is not without any dust, but controlled in a very small unit. Of course, the particles that meet the dust specifications in this specification are now very small compared to the commonly seen dust particle. However, for optical structures, even a small amount of dust can have a significant negative impact. Therefore, in the production of optical structure products, dust free is a certain requirement. The clean room in clean workshop is mainly used for the following three purposes:
Air clean workshop clean room: A clean room in clean workshop that has been completed and can be put into use. It has all relevant services and functions. However, there are no equipments operated by operators inside cleanroom.
Static clean workshop clean room: A clean room with complete functions and stable settings that can be used or in use according to the settings, but there are no operators inside the equipment.
Dynamic clean workshop clean room: A clean room in clean workshop that is in normal use, with complete service functions, equipment, and personnel; If needed, can engage in normal operation.
GMP requires pharmaceutical cleanrooms to have good production equipment, reasonable production processes, excellent quality management, and strict testing systems for purification, to ensure that product quality (including food safety and hygiene) meets regulatory requirements.
1. Minimize building area as much as possible
Workshops with cleanliness requirements not only have high investment, but also have high regular costs such as water, electricity, and gas. In general, the higher the cleanliness level of a workshop building, the greater the investment, energy consumption, and cost. Therefore, while meeting the production process requirements, the construction area of the clean workshop should be minimized as much as possible.
2. Strictly control the flow of people and logistics
Specialized pedestrian and logistics channels should be set up for pharmaceutical cleanrooms. Personnel should enter according to the prescribed cleaning procedures and strictly control the number of people. In addition to the standardized management of personnel entering and exiting the pharmaceutical cleanrooms for purification, the entry and exit of raw materials and equipment must also go through cleaning procedures to avoid affecting the air cleanliness of the clean room.
- Reasonable layout
(1) The equipment layout in the clean room should be as compact as possible to reduce the area of the clean room.
(2) The clean room doors are required to be airtight, and air locks are installed at the entrances and exits of people and cargo.
(3) The same level of clean rooms should be arranged together as much as possible.
(4) Different level of cleanrooms are arranged from lower to higher levels, and adjacent rooms should be equipped with partition doors. The corresponding pressure difference should be designed according to the cleanliness level, usually around 10Pa. The opening direction of the door should be towards rooms with higher cleanliness levels.
(5) The clean room should maintain positive pressure, and the space in clean room should be connected in order of cleanliness level, with corresponding pressure differences to prevent the air in low-level clean rooms from flowing back to high-level clean rooms. The net pressure difference between adjacent rooms with different air cleanliness levels should be greater than 5Pa, and the net pressure difference between clean room and outdoor atmosphere should be greater than 10Pa.
(6) Sterile area ultraviolet light is generally installed on the upper side of the sterile work area or at the entrance.
4. Pipeline should be concealed as much as possible
To meet the cleanliness level requirements of the workshop, various pipelines should be concealed as much as possible. The outer surface of the exposed pipeline should be smooth, and horizontal pipelines should be equipped with technical interlayer or technical mezzanine. Vertical pipelines passing through floors should be equipped with technical shaft.
5. Indoor decoration should bebenefical to cleaning
The walls, floors and top layer of the clean room should be flat and smooth, without cracks and static electricity accumulation, and the interface should be tight without particle shedding, and can withstand cleaning and disinfection. The junction between walls and ground, between walls, and between walls and ceilings should be curved or other measures should be taken to reduce dust accumulation and facilitate cleaning work.
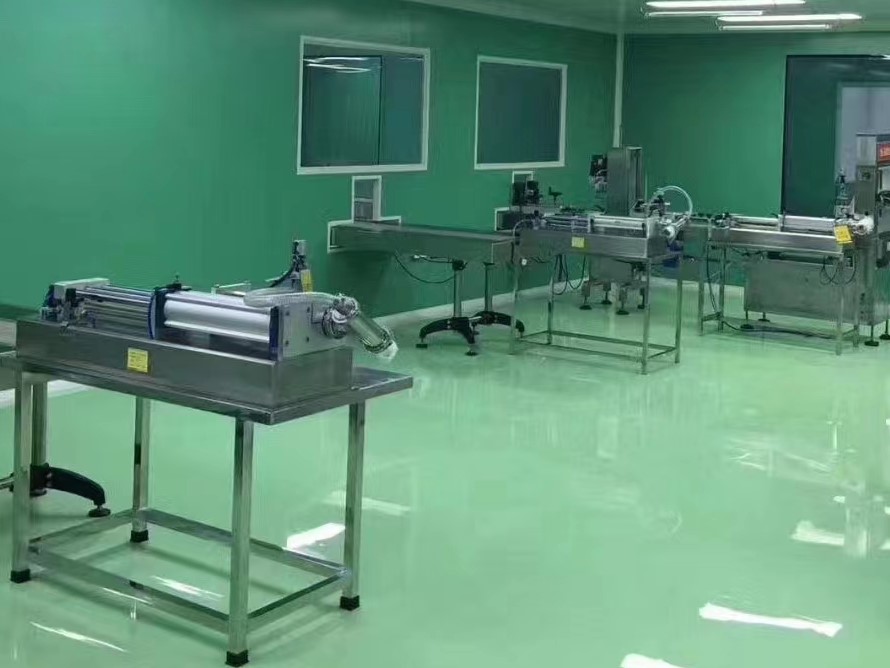
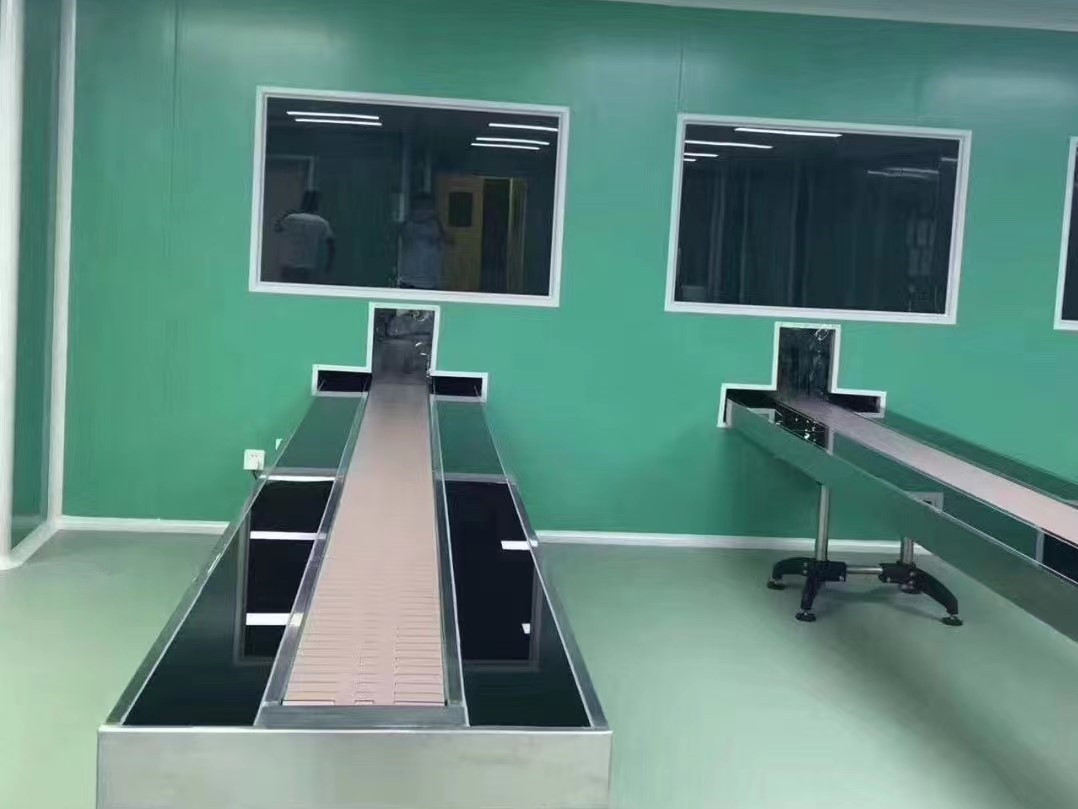
Post time: May-30-2023