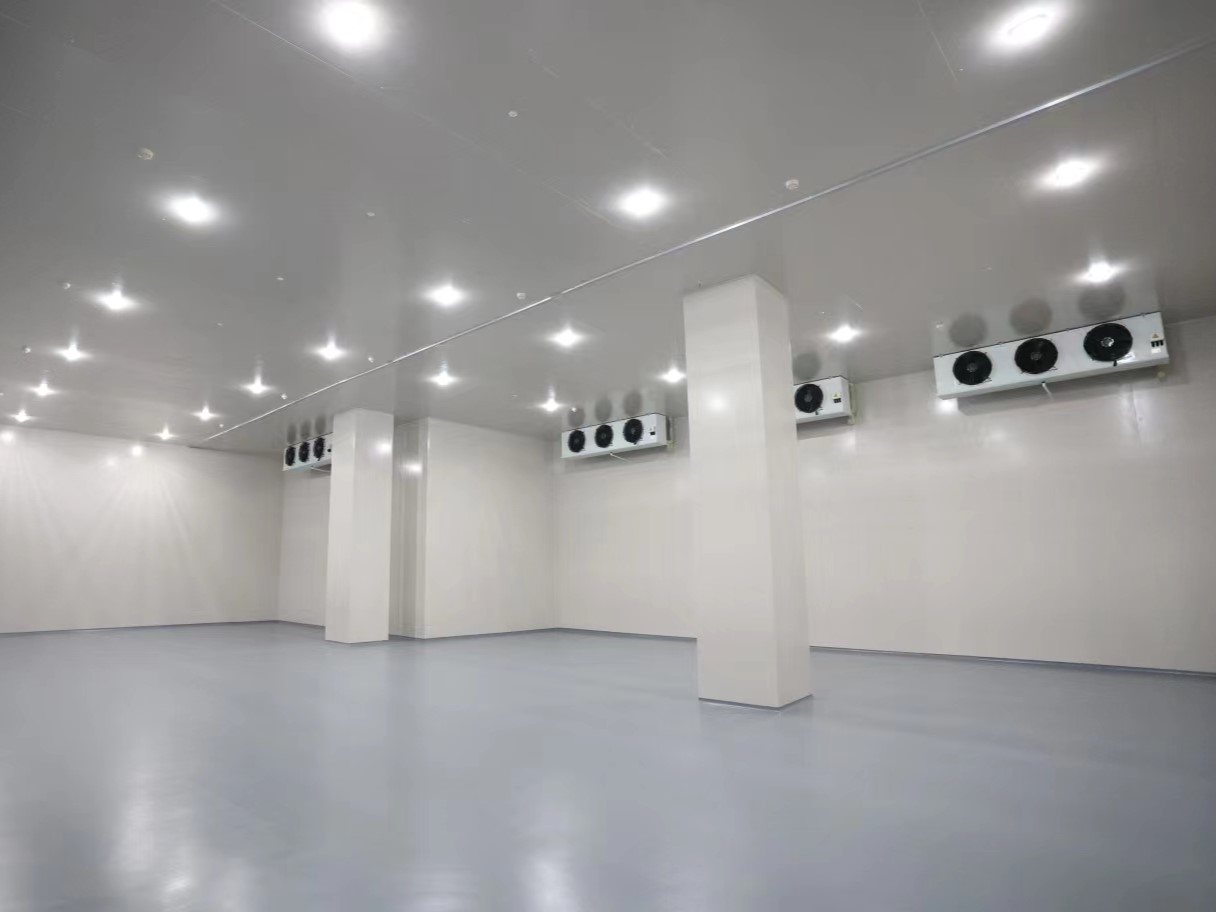
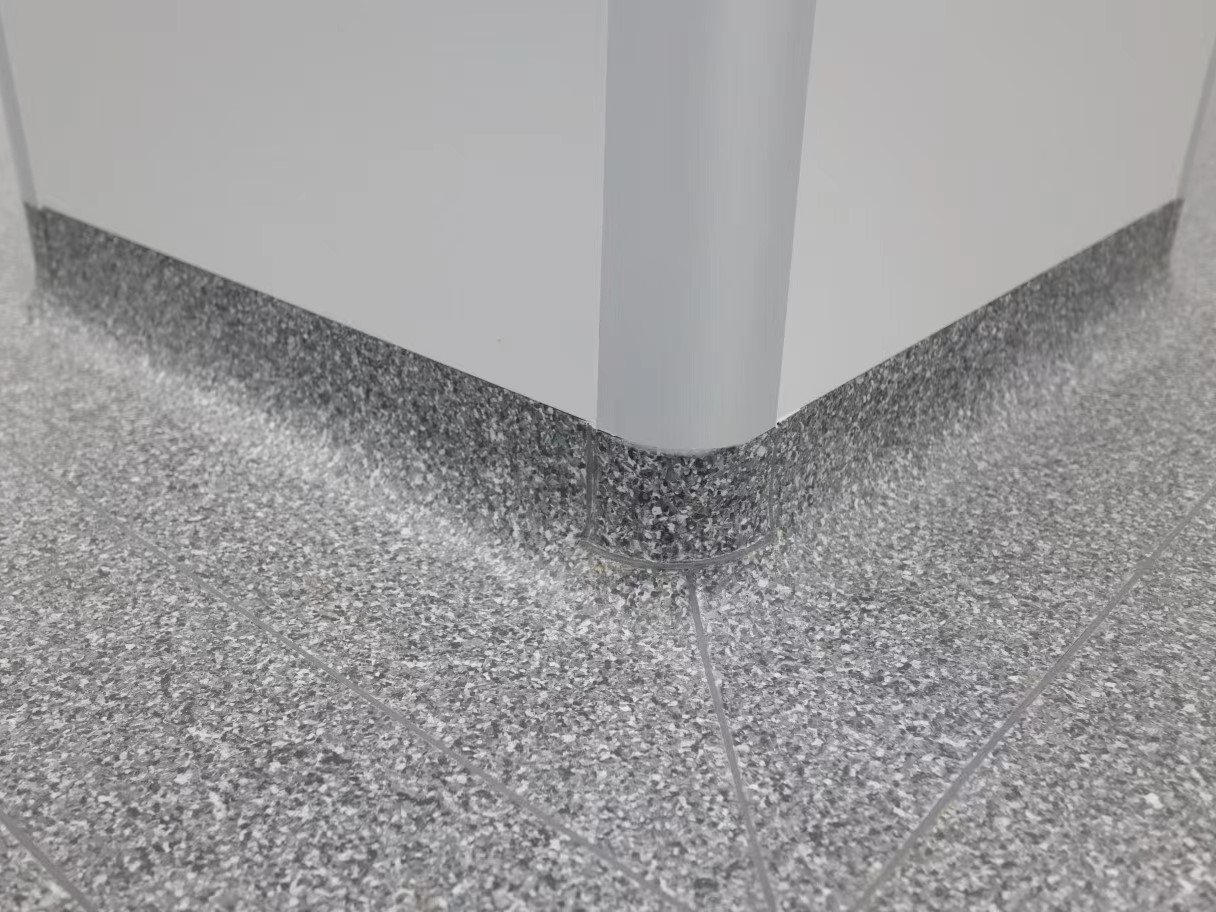
The fixed equipment in clean room that is closely related to the clean room environment, which is mainly the production process equipment in clean room and the purification air-conditioning system equipment to meet the cleanliness requirements. The maintenance and management of the operation process of the purification air-conditioning system equipment in clean room is domestic. There are similar provisions in relevant standards and specifications at home and abroad. Although there are some differences in conditions, application dates, laws and regulations of various countries or regions, and even differences in thinking and concepts, the proportion of similarities is still relatively high.
1. Under normal circumstances: the cleanliness in clean room must be consistent with the dust particle limit in air to meet the specified testing period. Clean rooms (areas) equal to or stricter than ISO 5 shall not exceed 6 months, while ISO 6~9 monitoring frequency of dust particle limits in air is required in GB 50073 for no more than 12 months. Cleanliness ISO 1 to 3 are cyclic monitoring, ISO 4 to 6 are once a week, and ISO 7 is once every 3 months, once every 6 months for ISO 8 and 9.
2. The air supply volume or air velocity and pressure difference of the clean room (area) proves that it continues to meet the specified testing period, which is 12 months for various cleanliness levels: GB 50073 requires that the temperature and humidity of the clean room be monitored frequently. Cleanliness ISO 1~3 is cyclic monitoring, other levels are 2 times per shift; About clean room pressure difference monitoring frequency, cleanliness ISO 1~3 is cyclic monitoring, ISO 4~6 is once a week , ISO 7 to 9 are once a month.
3. There are also requirements for the replacement of hepa filters in purification air-conditioning systems. The hepa air filters should be replaced in any of the following situations: the air flow speed drops to a relatively low limit, even after replacing the primary and medium air filters, the airflow speed still cannot be increased: the resistance of the hepa air filter reaches 1.5~2 times of the initial resistance; the hepa air filter has leaks that cannot be repaired.
4. The maintenance and repair process and methods of fixed equipment should be controlled and minimized possible contamination of the clean room environment. Clean room management regulations should document equipment maintenance and repair procedures to ensure the control of pollution in clean room environment, and a preventive maintenance work plan should be developed to achieve maintenance or replacement of equipment components before they become "sources of pollution."
5. Fixed equipment will wear out, become dirty, or emit pollution over time if not maintained. Preventive maintenance ensures that equipment does not become a source of pollution. When maintaining and repairing equipment, necessary protective/protective measures should be taken to avoid contaminating clean room.
6. Good maintenance should include decontamination of the outer surface. If the product production process requires it, the inner surface also needs to be decontaminated. Not only should the equipment be in working condition, but the steps to remove contamination on the inner and outer surfaces should also be consistent with the process requirements. The main measures to control the pollution generated during the maintenance of fixed equipment are: the equipment that needs to be repaired should be moved out of the district where it is located before repairing as much as possible to reduce the possibility of contamination; if necessary, the fixed equipment should be properly isolated from surrounding clean room. After that, major repair or maintenance work is carried out, or all products in process have been moved to the appropriate place; the clean room area adjacent to the equipment being repaired should be appropriately monitored to ensure effective control of contamination;
7. Maintenance personnel working in isolation area should not come into contact with those performing production or process processes. All personnel maintaining or repairing equipment in clean room should comply with the rules and regulations established for the area, including wearing clean room garment. Wear the required clean room garments in clean room and clean the area and equipment after the maintenance is completed.
8. Before technicians need to lie on their backs or lie down under the equipment to perform maintenance, they should first clarify the conditions of the equipment, production processes, etc., and effectively handle the situation of chemicals, acids, or biohazardous materials before working; measures should be taken to protect the clean clothes from coming into contact with lubricants or process chemicals and from being torn by the edges of the mirror. All tools, boxes and trolleys used for maintenance or repair work should be thoroughly cleaned before entering clean room. Rusted or corroded tools are not allowed. If these tools are used in a biological clean room, they may also need to be sterilized or disinfected; technicians should not place tools, spare parts, damaged parts, or cleaning supplies near work surfaces prepared for product and process materials.
9. During maintenance, attention should be paid to cleaning at all times to prevent the accumulation of contamination; gloves should be replaced regularly to avoid exposing the skin to clean surfaces due to damaged gloves; if necessary, use non-clean room gloves (such as acid-resistant, heat-resistant or scratch-resistant gloves), these gloves should be suitable for clean room, or should be worn over a pair of clean room gloves.
10. Use a vacuum cleaner when drilling and sawing. Maintenance and construction operations usually require the use of drills and saws. Special covers can be used to cover the tools and drill and pot working areas; open holes left after drilling on the ground, wall, side of equipment, or other such surfaces It should be properly sealed to prevent dirt from entering clean room. Sealing methods include the use of caulking materials, adhesives and special sealing plates. After repair work is completed, it may be necessary to verify the cleanliness of the surfaces of equipment that has been repaired or maintained.
Post time: Nov-17-2023