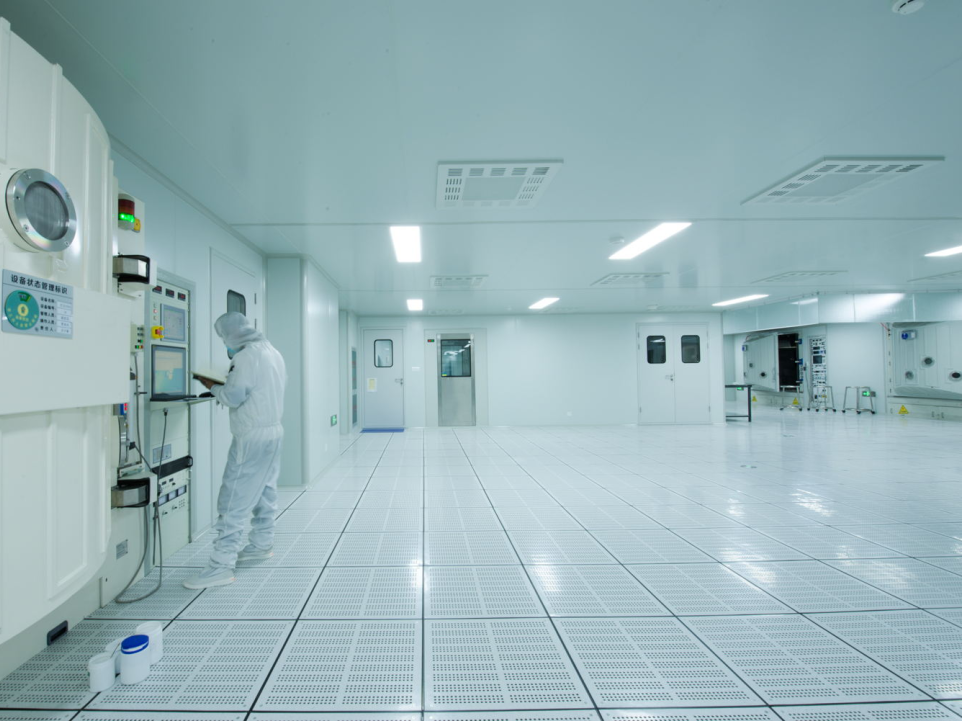
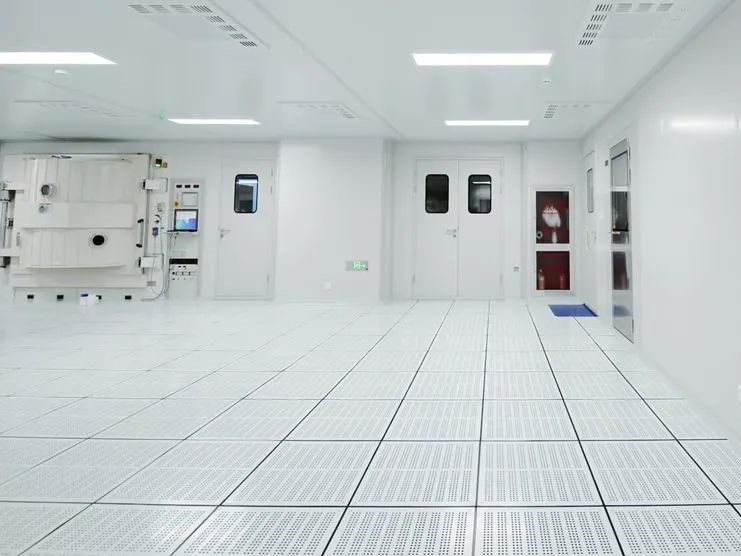
The clean room floor has various forms according to the production process requirements, cleanliness level and use functions of the product, mainly including terrazzo floor, coated floor (polyurethane coating, epoxy or polyester, etc), adhesive floor (polyethylene board, etc), high raised (movable) floor, etc.
In recent years, the construction of clean rooms in China has mainly used flooring, painting, coating (such as epoxy flooring), and high raised (movable) flooring. In the national standard "Code for Construction and Quality Acceptance of Clean Factories" (GB 51110), regulations and requirements are made for the construction of floor coating projects and high raised (movable) floors using water-based coatings, solvent based coatings, as well as dust and mold resistant coatings.
(1) The construction quality of the ground coating project in the clean room of the ground coating first depends on the "condition of the base layer". In relevant specifications, it is required to confirm that the maintenance of the base layer meets the regulations and requirements of relevant professional specifications and specific engineering design documents before conducting the ground coating construction, and to ensure that the cement, oil, and other residues on the base layer are cleaned; If the clean room is the bottom layer of the building, it should be confirmed that the waterproof layer has been prepared and accepted as qualified; After cleaning the dust, oil stains, residues, etc. on the surface of the base layer, a polishing machine and steel wire brush should be used to comprehensively polish, repair and level them, and then remove them with a vacuum cleaner; If the original ground of the renovation (expansion) is cleaned with paint, resin, or PVC, the surface of the base layer should be polished thoroughly, and putty or cement should be used to repair and level the surface of the base layer. When the surface of the base layer is concrete, the surface should be hard, dry, and free from honeycomb, powdery peeling, cracking, peeling, and other phenomena, and should be flat and smooth; When the base course is made of ceramic tile, terrazzo and steel plate, the height difference of adjacent plates shall not be greater than 1.0mm, and the plates shall not be loose or cracked.
The bonding layer of the surface layer of the ground coating project should be constructed according to the following requirements: there should be no production operations above or around the coating area, and effective dust prevention measures should be taken; The mixing of coatings should be measured according to the specified mix ratio and thoroughly stirred evenly; The thickness of the coating should be uniform, and there should be no omissions or whitening after application; At the junction with equipment and walls, paint shall not be adhered to relevant parts such as walls and equipment. The surface coating should strictly adhere to the following requirements: the surface coating must be carried out after the bonding layer is dried, and the construction environment temperature should be controlled between 5-35 ℃; The thickness and performance of the coating should meet the design requirements. The thickness deviation shall not exceed 0.2mm; Each ingredient must be used up within the specified time and recorded; The construction of the surface layer should be completed in one go. If the construction is carried out in installments, the joints should be minimal and set in hidden areas. The joints should be flat and smooth, and should not be separated or exposed; The surface of the surface layer should be free of cracks, bubbles, delamination, pits, and other phenomena; The volume resistance and surface resistance of the anti-static ground should meet the design requirements.
If the materials used for ground coating are not selected properly, it will directly or even seriously affect the air cleanliness of the clean room after operation, resulting in a decrease in product quality and even the inability to produce qualified products. Therefore, relevant regulations stipulate that properties such as mold proof, waterproof, easy to clean, wear-resistant, less dust, no dust accumulation, and no release of substances harmful to product quality should be selected. The color of the ground after painting should meet the engineering design requirements, and should be uniform in color, without color difference, pattern, etc.
(2) High raised floor is widely used in clean rooms in various industries, especially in unidirectional flow clean rooms. For example, different types of raised floor are often installed in vertical unidirectional flow clean rooms of ISO5 level and above to ensure airflow patterns and wind speed requirements. China can now produce various types of high raised floor products, including ventilated floors, anti-static floors, etc. During the construction of clean factory buildings, products are usually purchased from professional manufacturers. Therefore, in the national standard GB 51110, it is first required to check the factory certificate and load inspection report for high raised floor before construction, and each specification should have corresponding inspection reports to confirm that the high raised floor and its supporting structure meet the design and load-bearing requirements.
The building floor for laying high raised floors in the clean room should meet the following requirements: the ground elevation should meet the engineering design requirements; The surface of the ground should be flat, smooth, and dust-free, with a moisture content of no more than 8%, and should be coated according to the design requirements. For high raised floors with ventilation requirements, the opening rate and distribution, aperture or edge length on the surface layer should meet the design requirements. The surface layer and support components of elevated floors should be flat and solid, and should have performance such as wear resistance, mold resistance, moisture resistance, flame retardant or non combustible, pollution resistance, aging resistance, acid alkali resistance, and static electricity conductivity. The connection or bonding between high raised floor support poles and the building floor should be solid and reliable. The connecting metal components supporting the lower part of the upright pole should meet the design requirements, and the exposed threads of the fixing bolts should not be less than 3. The allowable slight deviation for the laying of high raised floor surface layer.
The installation of the corner plates of the high raised floor in the clean room should be cut and patched according to the actual situation on site, and adjustable supports and crossbars should be installed. The joints between the cutting edge and the wall should be filled with soft, dust-free materials. After the installation of the high raised floor, it should be ensured that there is no swing or sound when walking, and it is firm and reliable. The surface layer should be flat and clean, and the joints of the plates should be horizontal and vertical.
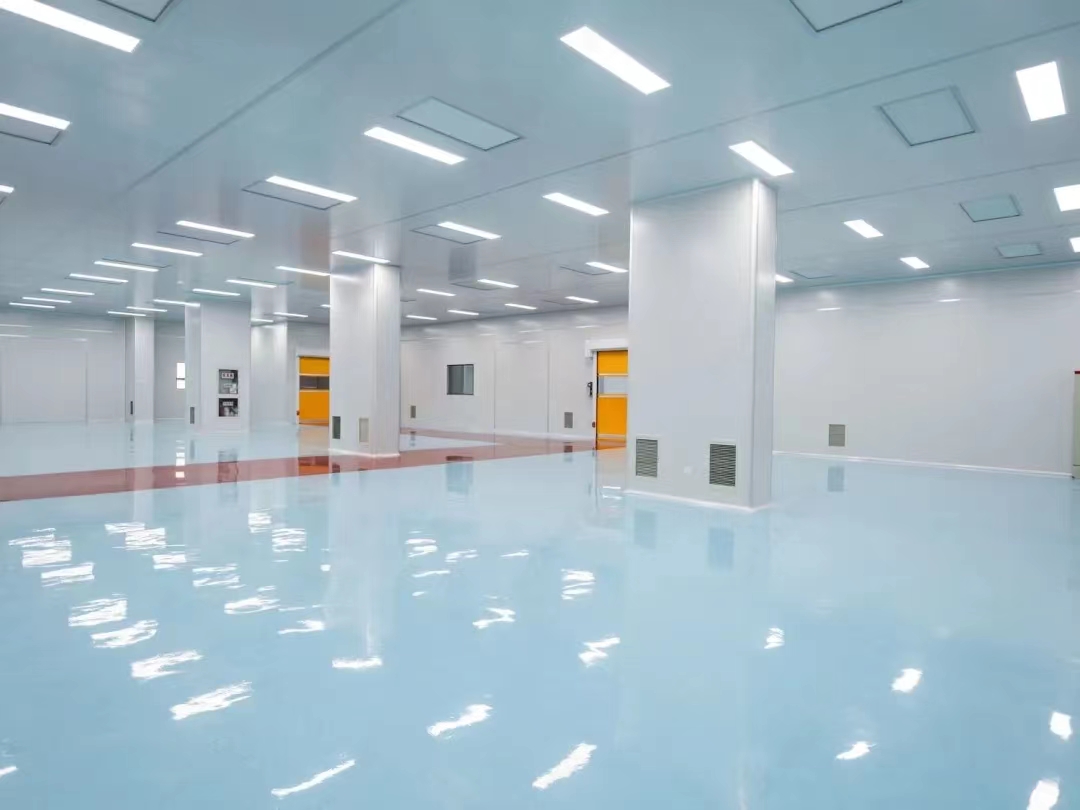

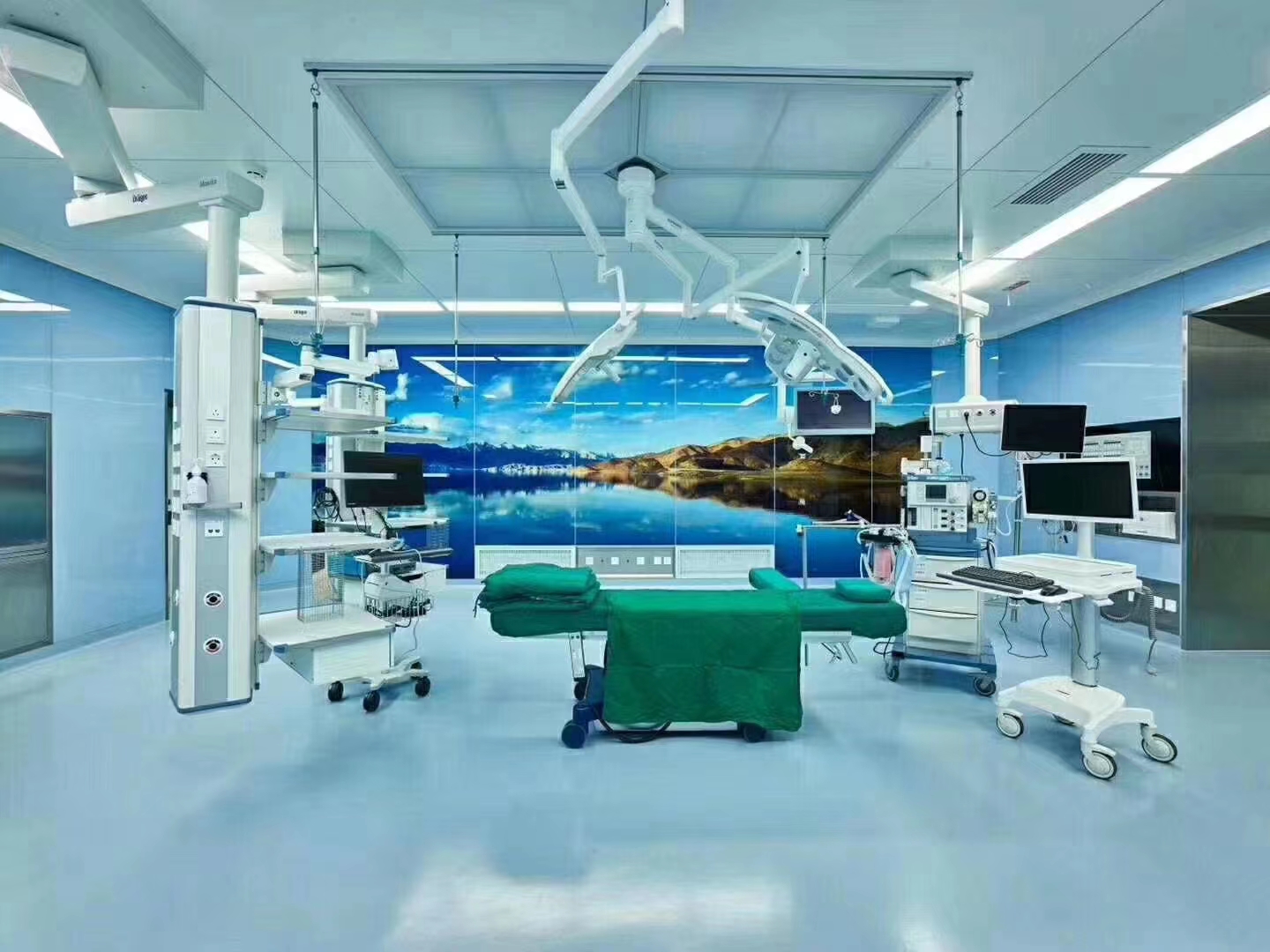
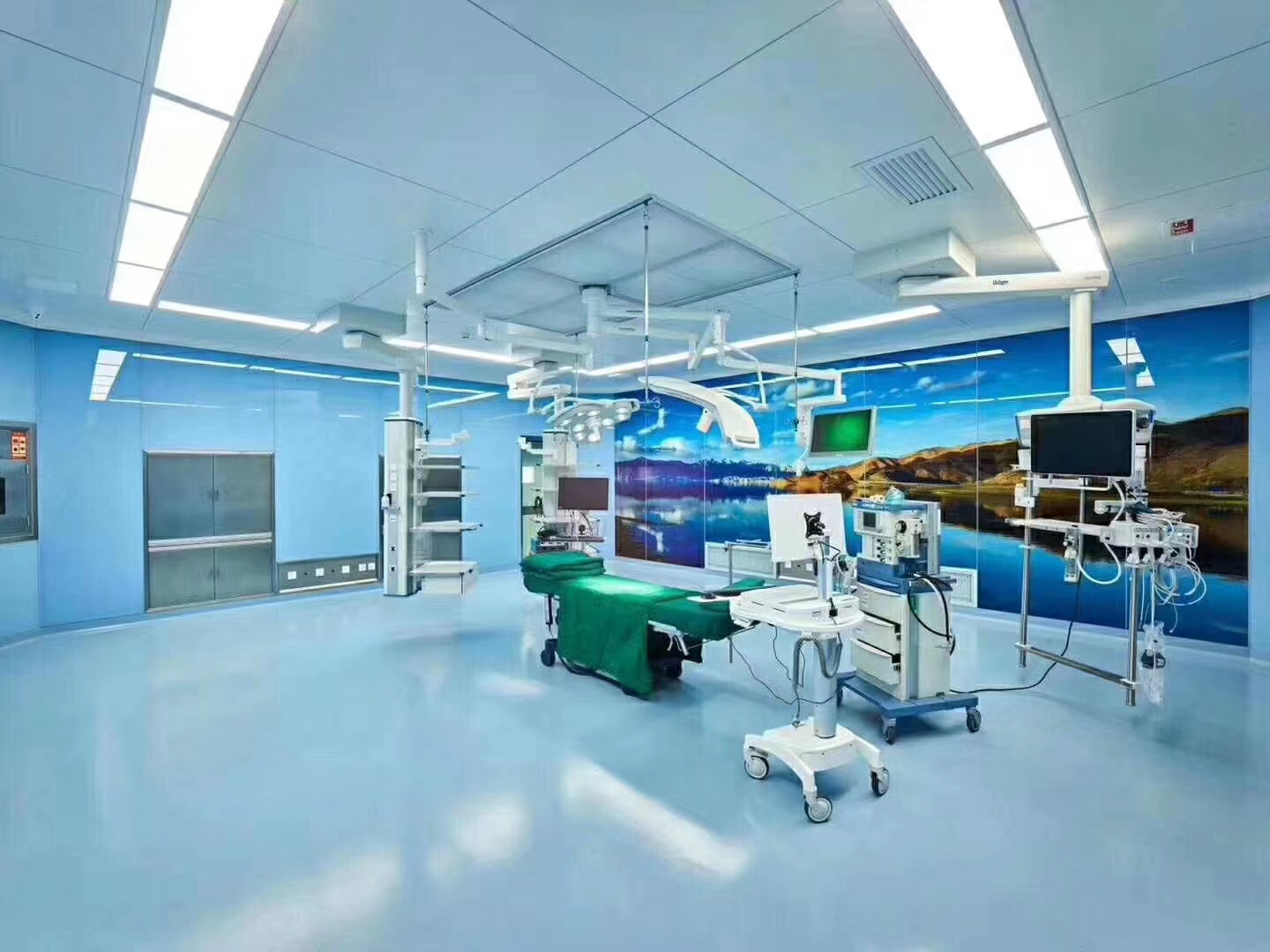
Post time: Jul-19-2023