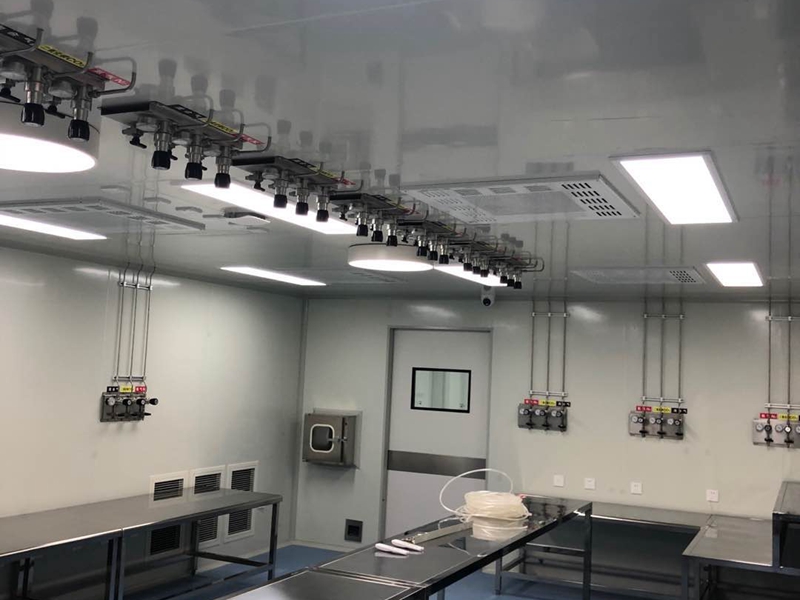
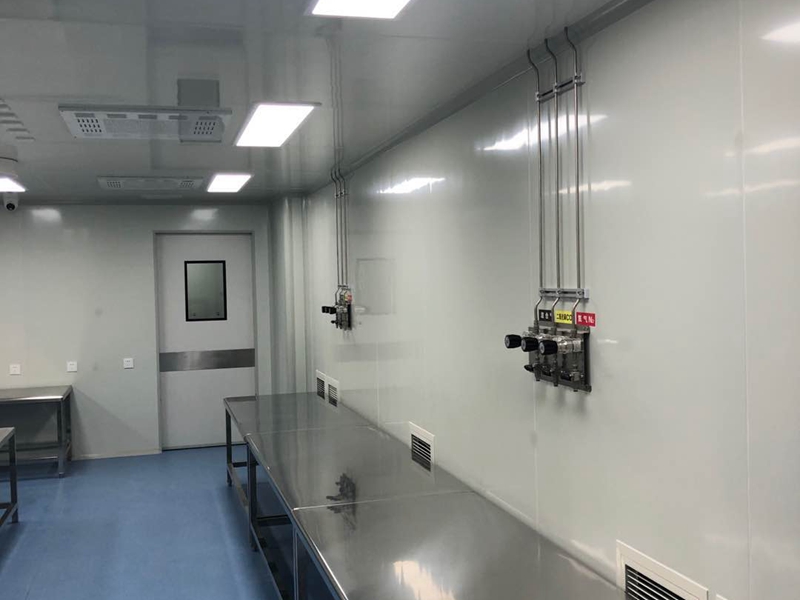
Biopharmaceuticals refer to medicines produced using biotechnology, such as biological preparations, biological products, biological drugs, etc. Since the purity, activity and stability of the product need to be ensured during the production of biopharmaceuticals, clean room technology needs to be used in production process to ensure product quality and safety. The design, construction and operation of biopharmaceutical GMP clean room require strict compliance with GMP specifications, including the control of clean room air cleanliness, temperature, humidity, pressure difference and other parameters, as well as the management of personnel, equipment, materials and waste in clean room. At the same time, advanced clean room technologies and equipment, such as hepa filter, air shower, clean bench, etc are also needed to ensure that air quality and microbial levels in clean room meet the requirements.
The design of gmp pharmaceutical clean room
1. Clean room design cannot meet the actual needs of production. For new clean room projects or large clean room renovation projects, owners generally tend to hire formal design institutes for design. For small and medium-sized clean room projects, considering the cost, The owner will usually sign a contract with an engineering company, and the engineering company will be responsible for design work.
2. To confuse the purpose of clean room testing, clean room performance testing and evaluation work is a very necessary step to measure whether the design requirements are met (acceptance testing) and to ensure the normal working status of the clean room (regular testing) when the clean room construction is completed. The acceptance test includes two stages: completion commissioning and comprehensive evaluation of the clean room's comprehensive performance.
3. Problems in clean room operation
①Air quality is not up to standard
②Irregular personnel operation
③Equipment maintenance is not timely
④Incomplete cleaning
⑤Improper waste disposal
⑥Influence of environmental factors
There are several important parameters to pay attention to when designing GMP pharmaceutical clean room.
1. Air cleanliness
The problem of how to correctly select parameters in the craft products workshop. According to different craft products, how to correctly select design parameters is a fundamental issue in design. GMP puts forward important indicators, that is, air cleanliness levels. The following table shows the air cleanliness levels specified in my country's 1998 GMP: At the same time, WHO (World Health Organization) and EU (European Union) both have different requirements for cleanliness levels. . The above levels have clearly indicated the number, size, and state of particles.
It can be seen that the cleanliness of high dust concentration is low, and the cleanliness of low dust concentration is high. Air cleanliness level is the core indicator for evaluating a clean air environment. For example, the 300,000-level standard comes from a new packaging specification issued by the Medical Bureau. It is currently inappropriate to be used in the main product process, but it works well when used in some auxiliary rooms.
2. Air exchange
The number of air changes in a general air-conditioning system is only 8 to 10 times per hour, while the number of air changes in an industrial clean room is 12 times at the lowest level and several hundred times at the highest level. Obviously, the difference in the number of air changes causes air volume Huge difference in energy consumption. In the design, on the basis of accurate positioning of cleanliness, sufficient air exchange times must be ensured. Otherwise, the operation results will not be up to standard, the clean room's anti-interference ability will be poor, the self-purification capacity will be correspondingly lengthened, and a series of problems will outweigh the gains.
3. Static pressure difference
There are a series of requirements such as the distance between clean rooms of different levels and non-clean rooms cannot be less than 5Pa, and the distance between clean rooms and outdoors cannot be less than 10Pa. The method to control the static pressure difference is mainly to supply a certain positive pressure air volume. The positive pressure devices commonly used in design are residual pressure valves, differential pressure electric air volume regulators and air damping layers installed at the return air outlets. In recent years, the method of not installing a positive pressure device but making the supply air volume larger than the return air volume and exhaust air volume during the initial commissioning is often used in the design, and the corresponding automatic control system can also achieve the same effect.
4. Airflow organization
The airflow organization pattern of a clean room is a key factor in ensuring the cleanliness level. The airflow organization form often adopted in current design is determined based on the cleanliness level. For example, class 300,000 clean room often use top-feed and top-return airflow, class 100000 and class 10000 cleanroom designs usually use an upper-side airflow and lower-side return airflow, and higher-level cleanrooms use horizontal or vertical unidirectional flow.
5. Temperature and humidity
In addition to special technology, from the perspective of heating, ventilation and air conditioning, it mainly maintains operator comfort, that is, appropriate temperature and humidity. In addition, there are several indicators that should attract our attention, such as the cross-sectional wind speed of the tuyere duct, noise, cross-sectional wind speed of the tuyere duct, noise, illumination, and the ratio of fresh air volume, etc. These aspects cannot be ignored in the design. consider.
Biopharmaceutical clean room design
Biological clean rooms are mainly divided into two categories; general biological clean rooms and biological safety clean rooms. HVAC engineering designers are usually exposed to the former, which mainly controls the pollution of operator by living particles. To some extent, it is an industrial clean room that adds sterilization processes. For industrial clean rooms, in professional design of HVAC system, an important means of controlling the cleanliness level is through filtration and positive pressure. For biological clean rooms, in addition to using the same methods as industrial clean rooms, it is also necessary to consider the biological safety aspect. Sometimes it is necessary to use negative pressure to prevent products from polluting the environment.
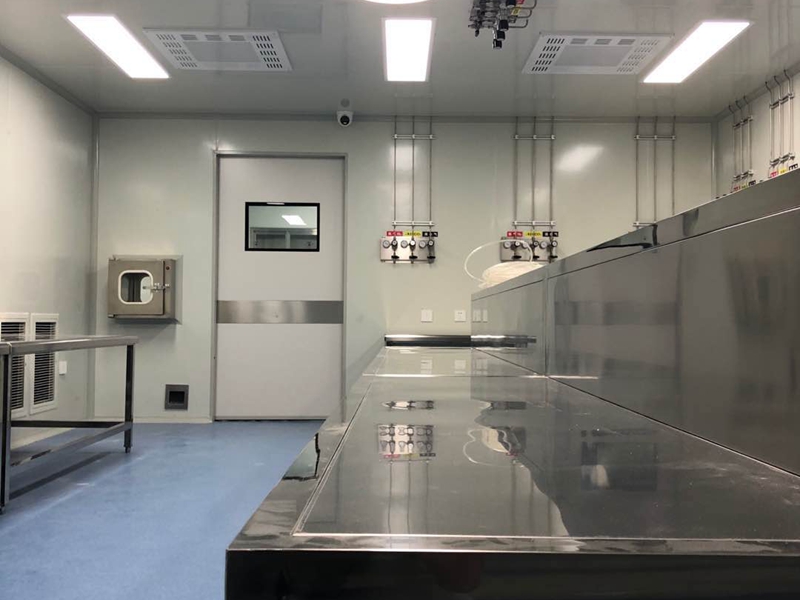
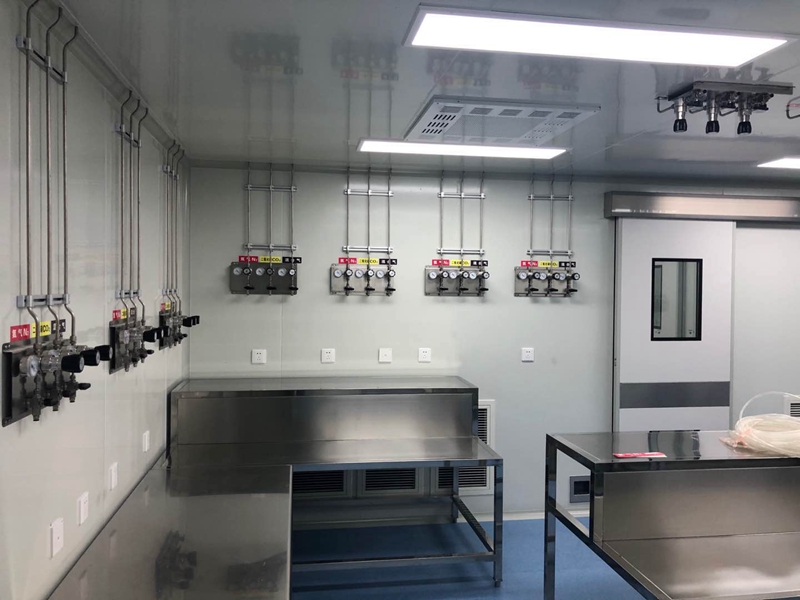
Post time: Dec-25-2023