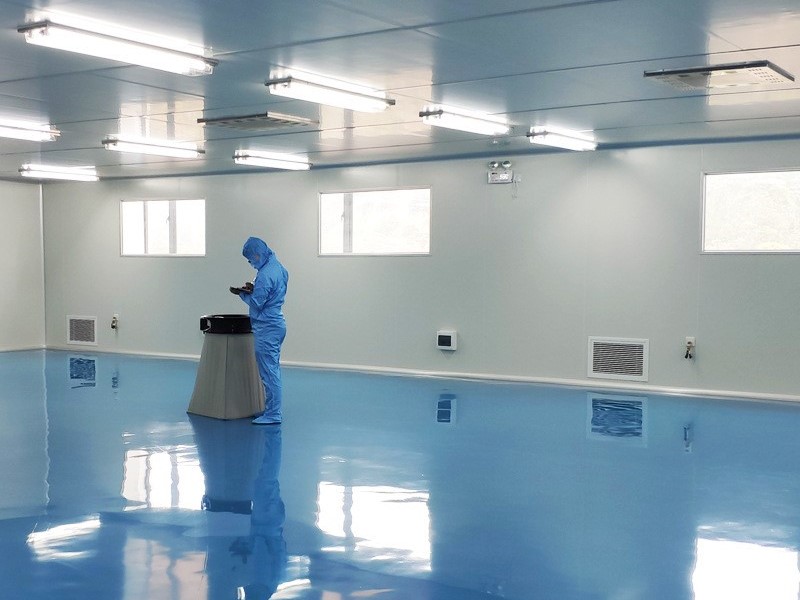
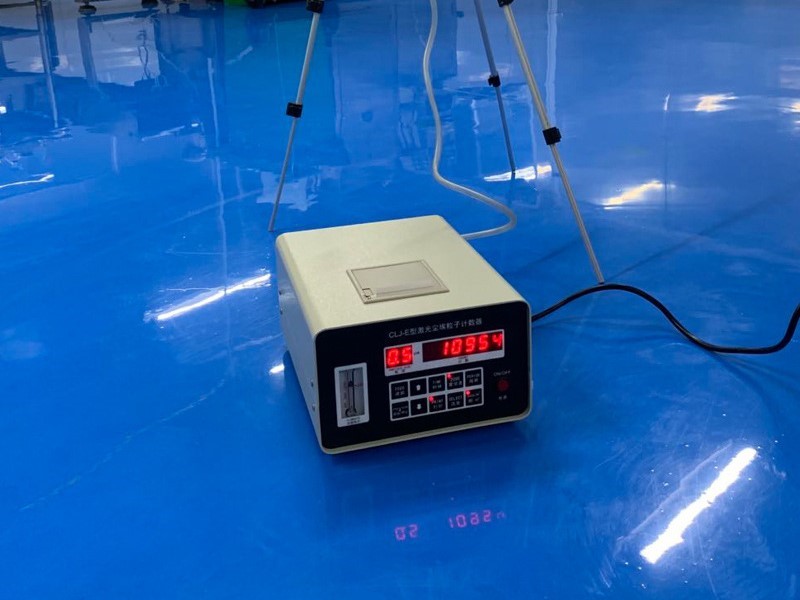
After the on-site commissioning with the class 10000 standard, the parameters such as air volume (number of air changes), pressure difference, and sedimentation bacteria all meet the design (GMP) requirements, and only one item of dust particle detection is unqualified (class 100000). The counter measurement results showed that large particles exceeded the standard, mainly 5 μm and 10 μm particles.
1. Failure analysis
The reason for large particles exceeding the standard generally occurs in high-cleanliness cleanrooms. If the purification effect of the cleanroom is not good, it will directly affect the test results; Through the analysis of air volume data and previous engineering experience, the theoretical test results of some rooms should be class 1000; The preliminary analysis is introduced as follows:
①. The cleaning work is not up to standard.
②. There is air leakage from the frame of the hepa filter.
③. The hepa filter has leakage.
④. Negative pressure in the cleanroom.
⑤. The air volume is not enough.
⑥. The filter of the air conditioning unit is clogged.
⑦. The fresh air filter is blocked.
Based on above analysis, the organization organized personnel to re-test the status of the cleanroom and found the air volume, pressure difference, etc to meet the design requirements. The cleanliness of all clean rooms was class 100000 and the 5 μm and 10 μm dust particles exceeded the standard and did not meet the class 10000 design requirements.
2. Analyze and eliminate possible faults one by one
In previous projects, there have been situations where insufficient pressure difference and reduced air supply volume occurred due to primary or medium-efficiency blockage in the fresh air filter or the unit. By inspecting the unit and measuring the air volume in the room, it was judged that items ④⑤⑥⑦ were not true; the remaining Next is the issue of indoor cleanliness and efficiency; there was indeed no cleaning done on site. When inspecting and analyzing the problem, workers had specially cleaned a clean room. The measurement results still showed that large particles exceeded the standard, and then opened the hepa box one by one to scan and filter. The scan results showed that one hepa filter was damaged in the middle, and the particle count measurement values of the frame between all other filters and the hepa box suddenly increased, especially for 5 μm and 10 μm particles.
3. Solution
Since the cause of the problem has been found, it is easy to solve. The hepa box used in this project are all bolt-pressed and locked filter structures. There is a gap of 1-2 cm between the filter frame and the inner wall of the hepa box. After filling the gaps with sealing strips and sealing them with neutral sealant, the cleanliness of the room is still class 100000.
4. Fault re-analysis
Now that the frame of the hepa box has been sealed, and the filter has been scanned, there is no leakage point in the filter, so the problem still occurs on the frame of the inner wall of the air vent. Then we scanned the frame again: The detection results of the inner wall frame of the hepa box. After passing the seal, re-inspect the gap of the inner wall of the hepa box and found that the large particles still exceed the standard. At first, we thought it was the eddy current phenomenon at the angle between the filter and the inner wall. We prepared to hang 1m film along the hepa filter frame. The left and right films are used as a shield, and then the cleanliness test is carried out under hepa filter. When preparing to paste the film, it is found that the inner wall has paint peeling phenomenon, and there is a whole gap in inner wall.
5. Handle dust from hepa box
Paste aluminum foil tape on the inner wall of the hepa box to reduce dust on the inner wall of the air port itself. After pasting aluminum foil tape, detect the number of dust particles along the hepa filter frame. After processing the frame detection, by comparing the particle counter detection results before and after processing, it can be clearly determined that the reason for the large particles exceeding the standard is caused by the dust scattered by the hepa box itself. After installing the diffuser cover, the clean room was re-tested.
6. Summary
The large particle exceeding the standard is rare in cleanroom project, and it can be completely avoided; through the summary of the problems in this cleanroom project, the project management needs to be strengthened in the future; this problem is due to the lax control of raw material procurement, which leads to scattered dust in hepa box. In addition, there were no gaps in hepa box or paint peeling during the installation process. In addition, there was no visual inspection before the filter was installed, and some bolts were not tightly locked when the filter was installed, all of which showed weaknesses in management. Although the main reason is dust from the hepa box, the construction of the clean room cannot be sloppy. Only by carrying out quality management and control throughout the process from the beginning of construction to the end of completion can the expected results be achieved in commissioning stage.
Post time: Sep-01-2023