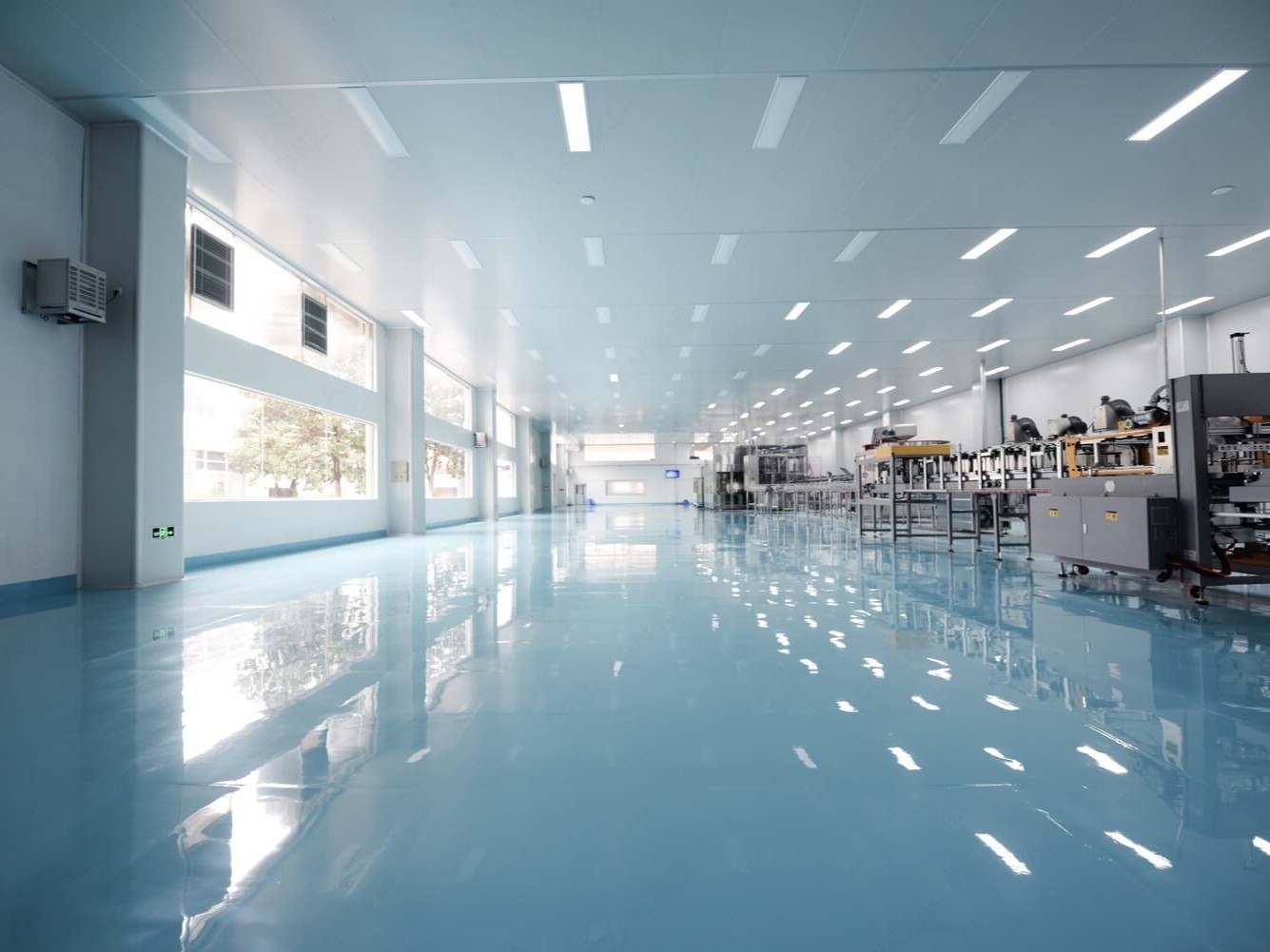
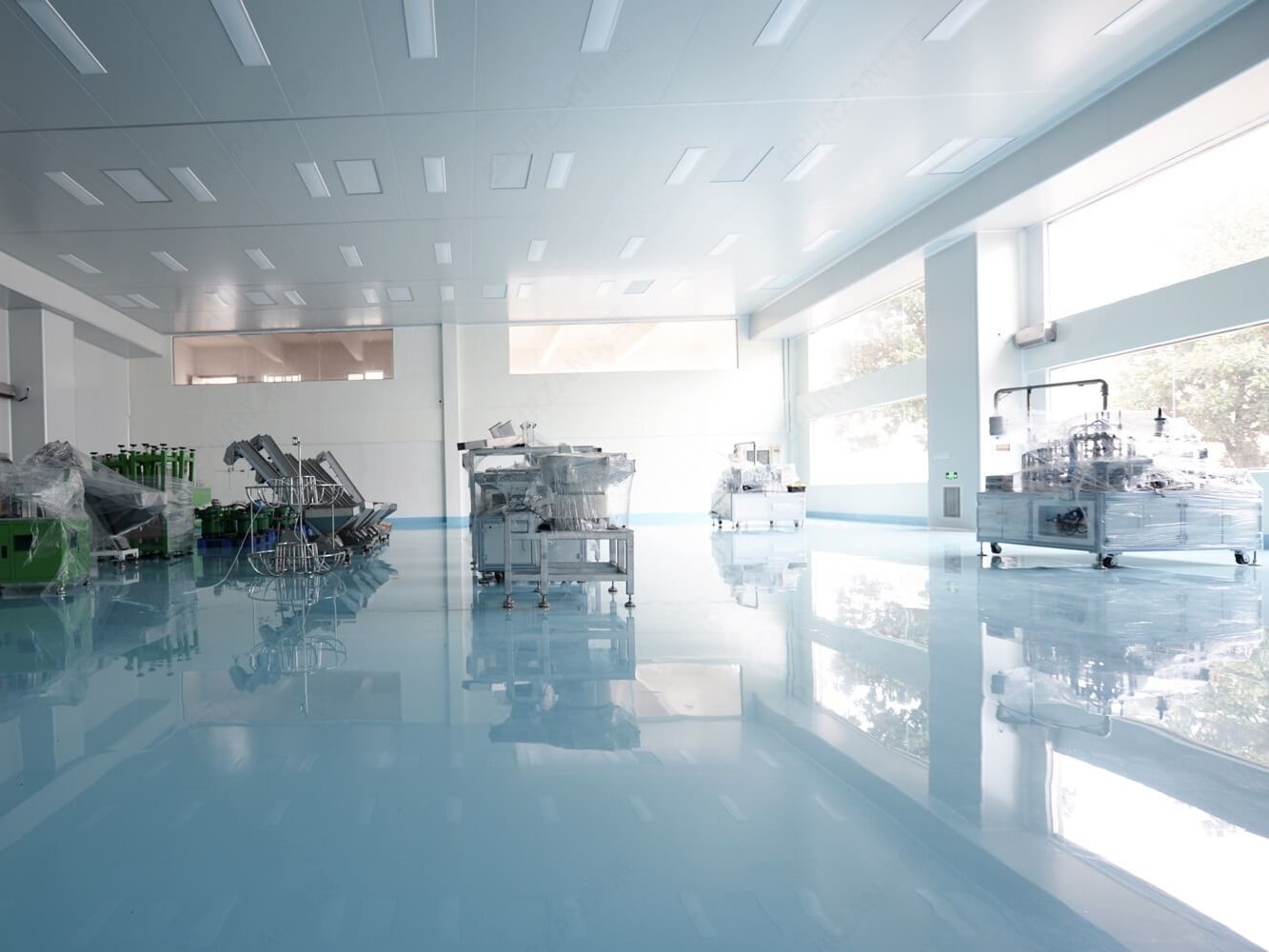
IS0 14644-5 requires that the installation of fixed equipment in clean rooms should be based on the design and function of clean room. The following details will be introduced below.
1. Equipment installation method: The ideal method is to close clean room during the equipment installation period, and have a door that can meet the viewing angle of the equipment or reserve a channel on the board to allow new equipment to pass through and enter clean room in order to prevent clean room near the installation period from being contaminated, protective measures should be taken to ensure that the clean room still meets its cleanliness requirements and the subsequent work required.
2. If the work in clean room cannot be stopped during each installation period, or if there are structures that need to be dismantled, the running clean room must be effectively isolated from the work area: temporary isolation walls or partitions can be used. In order not to hinder the installation work, there should be enough space around the equipment. If conditions permit, access to the isolation area can be through service channels or other non-critical areas: if this is not possible, measures should be taken to minimize the pollution impact caused by the installation work. The isolation area should maintain equal pressure or negative pressure. The clean air supply should be cut off in the high-rise area to avoid positive pressure on the surrounding clean rooms. If access to the isolation area is only through an adjacent clean room, sticky pads should be used to remove dirt from shoes.
3. After entering the high-altitude area, disposable boots or overshoes and one-piece work clothes can be used to avoid contaminating the clean clothes. These disposable items should be removed before leaving the quarantine area. Methods for monitoring the area around the isolation area during the equipment installation process should be developed and the frequency of monitoring should be determined to ensure that any contamination that may leak into the adjacent clean room is detected. After the isolation measures are set up, various required public service facilities, such as electricity, water, gas, vacuum, compressed air and wastewater pipelines, can be set up. Attention should be paid to controlling and isolating the smoke and debris generated by the operation as much as possible to avoid inadvertent spread to the surrounding clean room. It should also facilitate effective cleaning before removing the isolation barrier. After the public service facilities meet the usage requirements, the entire isolation area should be cleaned and decontaminated according to the prescribed cleaning procedures. All surfaces, including all walls, equipment (fixed and movable) and floors, should be vacuum cleaned, wiped and mopped, with special attention being paid to cleaning areas behind equipment guards and under equipment.
4. A preliminary test of equipment performance can be conducted based on the actual conditions of the clean room and installed equipment, but subsequent acceptance testing should be conducted when the clean environment conditions are fully met. Depending on the conditions at the installation site, you can begin to carefully dismantle the isolation wall; if the clean air supply has been turned off, restart it; the time for this stage of work should be carefully selected to minimize interference with the normal work of the clean room. At this time, it may be necessary to measure whether the concentration of airborne particles meets the specified requirements.
5. Cleaning and preparation of the interior of the equipment and key process chambers should be carried out under normal clean room conditions. All internal chambers and all surfaces that come into contact with the product or are involved in product transport must be wiped down to the required level of cleanliness. The cleaning sequence of the equipment should be from top to bottom. If particles are spread, larger particles will fall to the bottom of the equipment or the ground due to gravity. Clean the outer surface of the equipment from top to bottom. When necessary, surface particle detection should be carried out in areas where the product or production process requirements are critical.
6. In view of the characteristics of clean rooms, especially the large area, high investment, high output and very strict cleanliness requirements of high-tech clean rooms, the installation of production process equipment in this type of clean factory is more similar to that of ordinary clean rooms. To this end, the national standard "Code for Clean Factory Construction and Quality Acceptance" released in 2015 made some provisions for the installation of production process equipment in clean factories, mainly including the following.
①. In order to prevent contamination or even damage to the clean room that has undergone "empty" acceptance during the installation process of production process equipment, the installation process of the equipment must not have excessive vibration or tilt, and must not be divided and contaminate equipment surfaces.
②. In order to make the installation of production process equipment in the clean room orderly and without or with less sitting, and to follow the clean production management system in clean workshop, ensure that the installation process of the production equipment is protected according to the various "finished products" and "semi-finished products" accepted in "empty state", materials, machines, etc. that must be used in the installation process must not emit or may produce (including in the normal operation of the clean room for a long time) pollutants that are harmful to the products produced. Clean materials that are dust-free, rust-free, grease-free and do not produce dust during use should be used.
③. The building decoration surface of the clean room should be protected with clean, dust-free plates, films and other materials; the equipment backing plate should be made according to the design or equipment technical document requirements. If there are no requirements, stainless steel plates or plastic plates should be used. Carbon steel profiles used for independent foundations and floor reinforcements should be treated with anti-corrosion, and the surface should be flat and smooth; elastic sealing materials used for caulking.
④. Materials should be marked with ingredients, varieties, date of manufacture, storage validity period, construction method instructions and product qualification certificates. Machinery and tools used in clean rooms must not be moved to non-clean rooms for use. Machinery and tools must not be moved to the clean room for use. Machinery and tools used in the clean area should ensure that the exposed parts of the machine do not produce dust or take measures to prevent dust from polluting the environment. Commonly used machines and tools should be cleaned in the airlock before being moved to the clean area. , should meet the requirements of being oil-free, dirt-free, dust-free, and rust-free, and should be moved after passing the inspection and affixing a "Clean" or "Clean Area Only" sign.
⑤. The production process equipment in the clean room needs to be installed on "specific floors" such as raised floors. The equipment foundation should generally be set on the lower technical mezzanine floor or on the cement porous plate; the activities that need to be dismantled to install the foundation The structure of the floor after being cut with a hand-held electric saw should be reinforced, and its load-bearing capacity should not be lower than the original load-bearing capacity. When an independent foundation of a steel frame structure is used, it should be made of galvanized material or stainless steel, and the exposed surface should be flat and smooth.
⑥. When the installation process of production process equipment in clean room requires opening holes in wall panels, suspended ceilings and raised floors, the drilling operations must not divide or contaminate the surfaces of wall panels and suspended ceiling panels that need to be retained. After the opening of the raised floor when the foundation cannot be installed in time, safety guardrails and hazard signs should be installed; after the production equipment is installed, the gap around the hole should be sealed, and the equipment and sealing components should be in flexible contact, and the connection between the sealing component and the wall plate should be tight and firm; the sealing surface on one side of the workroom should be flat and smooth.
Post time: Sep-06-2023