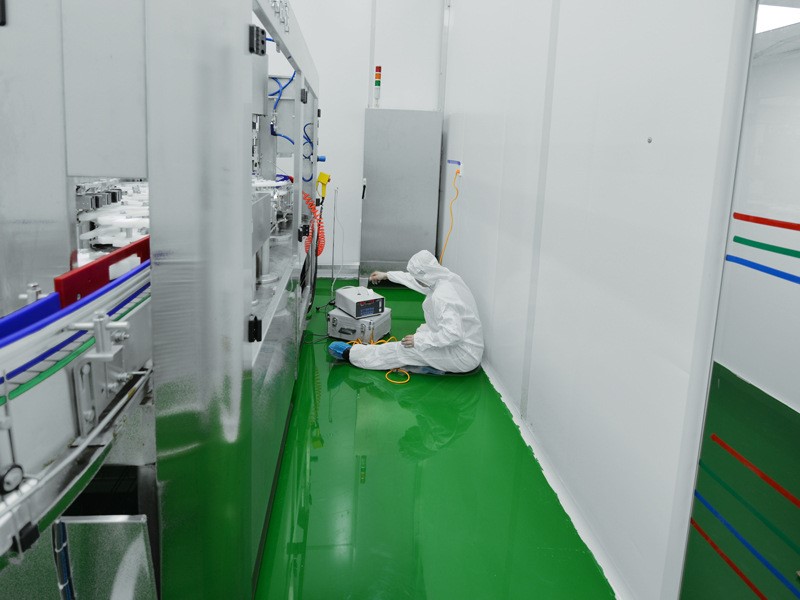
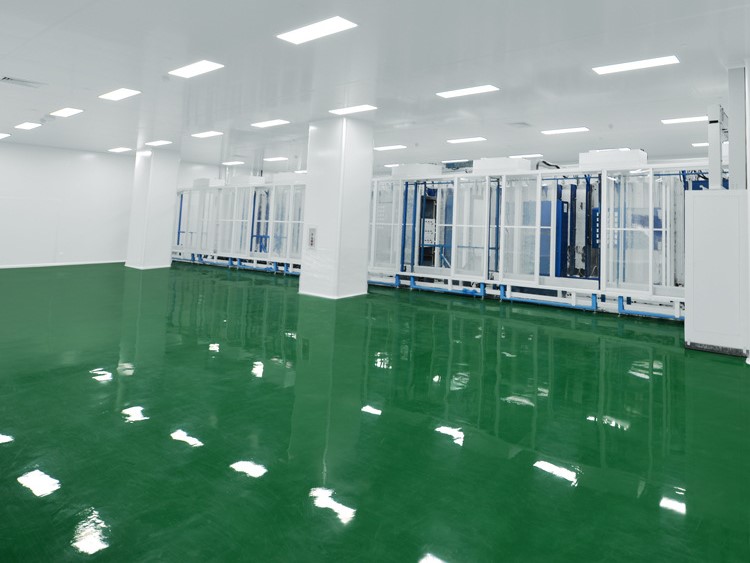
Usually the scope of clean room testing includes: clean room environmental grade assessment, engineering acceptance testing, including food, health products, cosmetics, bottled water, milk production workshop, electronic product production workshop, GMP workshop, hospital operating room, animal laboratory , biosafety laboratories, biosafety cabinets, clean benches, dust-free workshops, sterile workshops, etc.
Clean room testing content: air velocity and air volume, number of air changes, temperature and humidity, pressure difference, suspended dust particles, floating bacteria, settled bacteria, noise, illumination, etc. For details, please refer to the relevant standards for clean room testing.
The detection of clean rooms should clearly identify their occupancy status. Different statuses will result in different testing results. According to the "Clean Room Design Code" (GB 50073-2001), clean room testing is divided into three states: empty state, static state and dynamic state.
(1) Empty state: The facility has been built, all power is connected and running, but there are no production equipment, materials and staff.
(2) Static state has been built, the production equipment has been installed, and is operating as agreed by the owner and supplier, but there are no production staff.
(3) Dynamic state operates in a specified state, has specified staff present, and performs work in an agreed-upon state.
1. Air velocity, air volume and number of air changes
The cleanliness of clean rooms and clean areas is mainly achieved by sending in a sufficient amount of clean air to displace and dilute the particulate pollutants generated in the room. Therefore, it is very necessary to measure the air supply volume, average wind speed, air supply uniformity, air flow direction and flow pattern of clean rooms or clean facilities.
For the completion acceptance of clean room projects, my country's "Clean Room Construction and Acceptance Specifications" (JGJ 71-1990) clearly stipulates that testing and adjustment should be carried out in the empty state or static state. This regulation can more timely and objectively evaluate the quality of the project, and can also avoid disputes over project closure due to failure to achieve dynamic results as scheduled.
In the actual completion inspection, static conditions are common and empty conditions are rare. Because some of the process equipment in the clean room must be in place in advance. Before cleanliness testing, process equipment needs to be wiped carefully to avoid affecting the test data. The regulations in the "Clean Room Construction and Acceptance Specifications" (GB50591-2010) implemented on February 1, 2011 are more specific: "16.1.2 The occupancy status of the clean room during inspection is divided as follows: the engineering adjustment test should be empty, The inspection and daily routine inspection for project acceptance should be empty or static, while the inspection and monitoring for use acceptance should be dynamic. When necessary, the inspection status can also be determined through negotiation between the builder (user) and the inspection party."
The directional flow mainly relies on clean airflow to push and displace the polluted air in the room and area to maintain the cleanliness of the room and area. Therefore, its air supply section wind speed and uniformity are important parameters that affect cleanliness. Higher and more uniform cross-sectional wind speeds can remove pollutants produced by indoor processes faster and more effectively, so they are the clean room testing items we mainly focus on.
Non-unidirectional flow mainly relies on the incoming clean air to dilute and dilute the pollutants in the room and area to maintain its cleanliness. The results indicate that the greater the number of air changes and the reasonable airflow pattern, the better the dilution effect will be. Therefore, the air supply volume and corresponding air changes in non-single-phase flow clean rooms and clean areas are air flow test items that have attracted much attention.
2. Temperature and humidity
Temperature and humidity measurement in clean rooms or clean workshops can generally be divided into two levels: general testing and comprehensive testing. The completion acceptance test in empty state is more suitable for the next grade; the comprehensive performance test in the static or dynamic state is more suitable for the next grade. This kind of test is suitable for occasions with strict requirements on temperature and humidity.
This test is performed after the airflow uniformity test and the air conditioning system adjustment. During this test period, the air conditioning system worked well and various conditions have stabilized. It is a minimum to install a humidity sensor in each humidity control zone, and give the sensor enough stabilization time. The measurement should be suitable for actual use until the sensor is stable before starting the measurement. The measurement time must be more than 5 minutes.
3. Pressure difference
This kind of testing is to verify the ability to maintain a certain pressure difference between the completed facility and the surrounding environment, and between each space in the facility. This detection applies to all 3 occupancy states. This testing is indispensable. The detection of pressure difference should be carried out with all doors closed, starting from high pressure to low pressure, starting from the inner room far away from the outside in terms of layout, and then testing outwards in sequence. Clean rooms of different grades with interconnected holes have only reasonable airflow directions at the entrances.
Pressure difference testing requirements:
(1) When all doors in clean area are required to be closed, the static pressure difference is measured.
(2) In a clean room, proceed in order from high to low cleanliness until a room with direct access to outside is detected.
(3) When there is no air flow in room, the measuring tube mouth should be set at any position, and the measuring tube mouth surface should be parallel to air flow streamline.
(4) The measured and recorded data should be accurate to 1.0Pa.
Pressure difference detection steps:
(1) Close all doors.
(2) Use a differential pressure gauge to measure the pressure difference between each clean room, between clean room corridors, and between the corridor and the outside world.
(3) All data should be recorded.
Pressure difference standard requirements:
(1) The static pressure difference between clean rooms or clean areas of different levels and non-clean rooms (areas) is required to be more than 5Pa.
(2) The static pressure difference between the clean room (area) and the outdoors is required to be more than 10Pa.
(3) For unidirectional flow clean rooms with air cleanliness levels stricter than ISO 5 (Class100), when the door is opened, the dust concentration on indoor working surface 0.6m inside the door should be less than the dust concentration limit of the corresponding level.
(4) If the above standard requirements are not met, the fresh air volume and exhaust air volume should be readjusted until qualified.
4. Suspended particles
(1) Indoor testers must wear clean clothes and should be smaller than two people. They should be located on the downwind side of the test point and away from the test point. They should move lightly when changing points to avoid increasing the interference of staff on indoor cleanliness.
(2) The equipment must be used within the calibration period.
(3) The equipment must be cleared before and after testing.
(4) In the unidirectional flow area, the selected sampling probe should be close to dynamic sampling, and the deviation of the air velocity entering the sampling probe and the air velocity being sampled should be less than 20%. If this is not done, the sampling port should face the main direction of air flow. For non-unidirectional flow sampling points, the sampling port should be vertically upward.
(5) The connecting pipe from the sampling port to the dust particle counter sensor should be as short as possible.
5. Floating bacteria
The number of low-position sampling points corresponds to the number of suspended particle sampling points. The measuring points in the work area are about 0.8-1.2m above the ground. The measuring points at the air supply outlets are about 30cm away from the air supply surface. Measuring points can be added at key equipment or key work activity ranges. , each sampling point is usually sampled once.
6. Settled bacteria
Work at a distance of 0.8-1.2m from the ground. Place the prepared Petri dish at the sampling point. Open the Petri dish cover. After the specified time, cover the Petri dish again. Place the Petri dish in a constant temperature incubator for cultivation. The time required over 48 hours, each batch must have a control test to check for contamination of the culture medium.
7. Noise
If the measurement height is about 1.2 meters from the ground and the area of the clean room is within 15 square meters, only one point in the center of the room can be measured; if the area is more than 15 square meters, four diagonal points should also be measured, one 1 point from the side wall, measuring points facing each corner.
8. Illumination
The measuring point surface is about 0.8 meters away from the ground, and the points are arranged 2 meters apart. For rooms within 30 square meters, the measuring points are 0.5 meters away from the side wall. For rooms larger than 30 square meters, the measuring points are 1 meter away from the wall.
Post time: Sep-14-2023