The class 100000 clean room project of a dust free workshop refers to the use of a series of technologies and control measures to produce products that require a high cleanliness environment in a workshop space with a cleanliness level of 100000.
This article will provide a detailed introduction to the relevant knowledge of the class 100000 clean room project in a dust free workshop.
Concept of class 100000 clean room project
A dust free workshop refers to a workshop that designs and controls the cleanliness, temperature, humidity, airflow, etc of the workshop environment to meet specific requirements, in order to ensure the cleanliness and quality of production equipment, personnel, and manufactured products.
Standard for class 100000 clean room
Class 100000 clean room means that the number of dust particles in each cubic meter of air is less than 100000, which meets the standard of class 100000 air cleanliness.
Key design elements of class 100000 clean room project
1. Ground treatment
Choose flooring materials that are anti-static, slip resistant, wear-resistant, and easy to clean.
2. Door and window design
Choose door and window materials with good airtightness and minimal impact on workshop cleanliness.
3. HVAC system
The air handling system is the most important part. The system should consist of primary filters, intermediate filters, and hepa filters to ensure that all air used in the manufacturing process is close to clean air.
4. Clean area
Clean and non clean areas should be isolated to ensure that the air within a certain range can be controlled.
Implementation process of class 100000 clean room project
1. Calculate spatial cleanliness
Firstly, use testing instruments to calculate the cleanliness of the original environment, as well as the content of dust, mold, etc.
2. Develop design standards
Based on the needs of product production, fully utilize production conditions and develop design standards that meet production requirements.
3. Environmental simulation
Simulate the workshop usage environment, test the air purification treatment equipment, test the purification effect of the system, and reduce the reduction of target substances such as particles, bacteria, and odors.
4. Equipment installation and debugging
Install air purification treatment equipment and conduct debugging to ensure stable operation of the system.
5. Environmental testing
Use air detection instruments to test the cleanliness, particles, bacteria and other indicators of the workshop, and confirm that the air quality in the workshop meets the requirements.
6. Classification of clean areas
According to design requirements, the workshop is divided into clean and non clean areas to ensure the cleanliness of the entire workshop space.
Advantages of Clean Workshop Purification Technology
1. Improve production efficiency
In a dust free workshop environment, the production process of products is easier for producers to focus on production than in a typical production workshop. Due to better air quality, employees' physical, emotional, and mental levels can be guaranteed, thereby improving production efficiency.
2. Increase product quality stability
The quality of products produced in a dust free workshop environment will be more stable, as products produced in a clean environment often have better stability and consistency.
3. Reduce production costs
Although the cost of constructing a dust free workshop is relatively high, it can reduce errors in the production process, reduce the breakeven point, and thus reduce overall production costs.
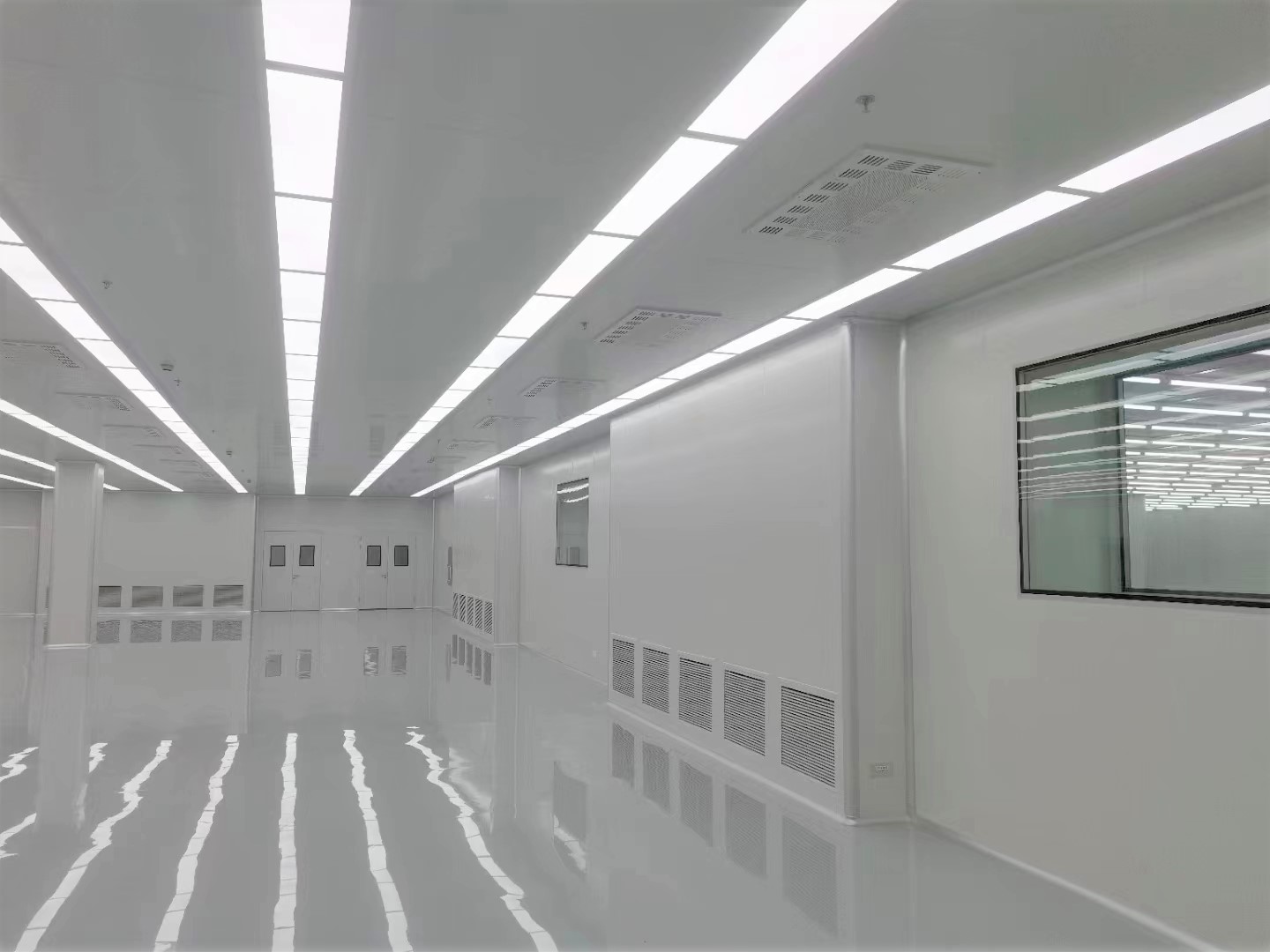
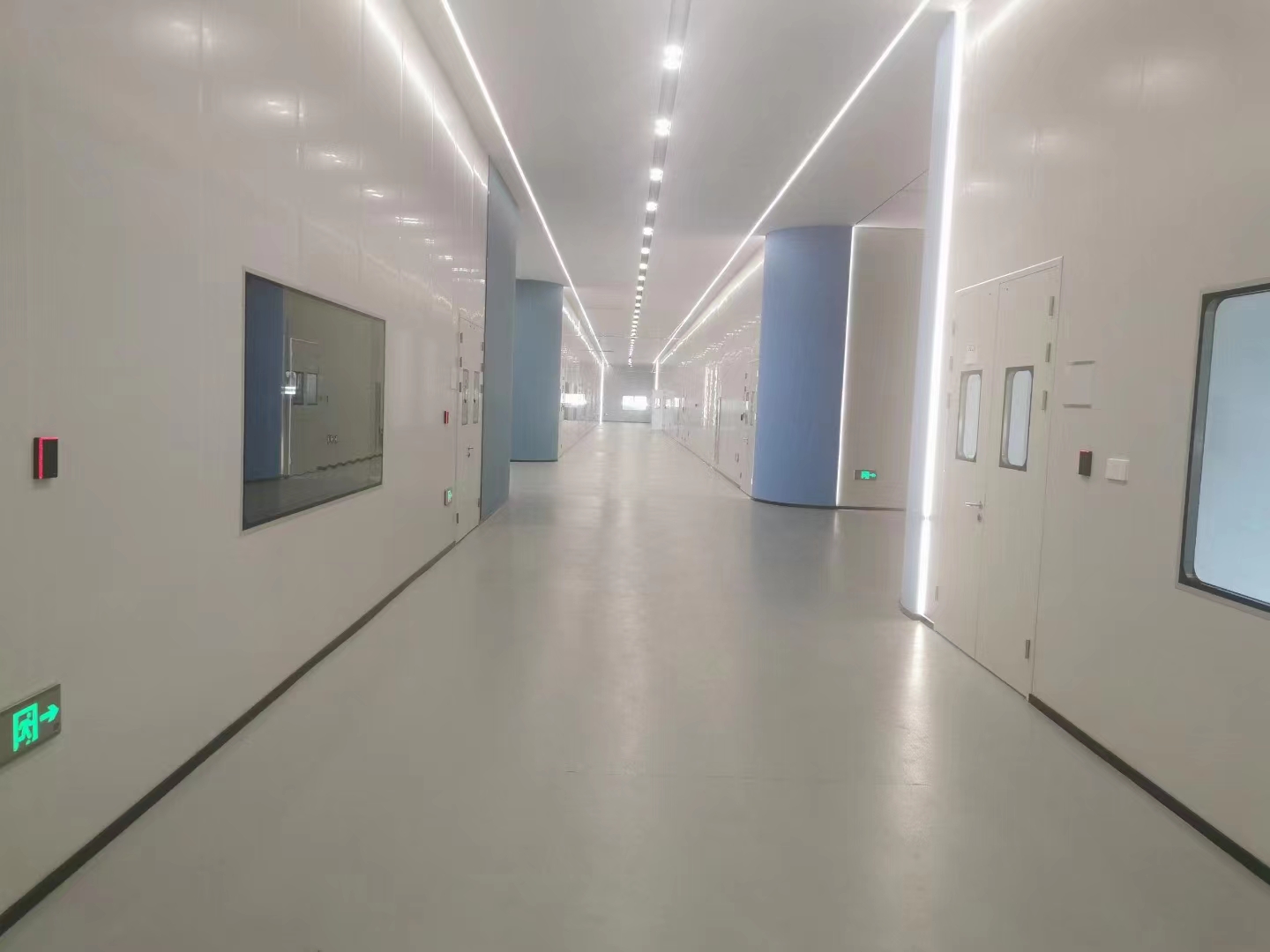
Post time: Jul-12-2023