When designing a food GMP clean room, the flow for people and material should be separated, so that even if there is contamination on the body, it will not be transmitted to the product, and the same is true for the product.
Principles to note
1. Operators and materials entering clean area cannot share the same entrance. Operator and material entry channels should be provided separately. If raw materials and auxiliary materials and packaging materials that directly come into contact with food are reliably packaged, will not cause contamination to each other, and the process flow is reasonable, in principle, one entrance can be used. For materials and waste that are likely to pollute the environment, such as activated carbon and residues used or generated during the production process, special entrances and exits should be set up to avoid contamination of raw materials, auxiliary materials or inner packaging materials. It is best to set up separate entrances and exits for materials entering clean area and finished products shipped out of the clean area.
2. Operators and materials entering clean area should set up their own purification rooms or take corresponding purification measures. For example, operators can enter the clean production area through the airlock after taking a shower, wearing clean work clothes (including work caps, work shoes, gloves, masks, etc.), air showering, washing hands, and hand disinfection. Materials can enter clean area through the air lock or pass box after taking off outer packaging, air showering, surface cleaning, and disinfection.
3. In order to avoid contamination of food by external factors, when designing the layout of process equipment, only production-related equipment, facilities and material storage rooms should be set up in the clean production area. Public auxiliary facilities such as compressors, cylinders, vacuum pumps, dust removal equipment, dehumidification equipment, exhaust fans for compressed gas should be arranged in the general production area as long as the process requirements permit. In order to effectively prevent cross-contamination between foods, foods of different specifications and varieties cannot be produced in the same clean room at the same time. For this reason, its production equipment should be arranged in a separate clean room.
4. When designing a passage in clean area, ensure that the passage directly reaches each production position, intermediate or packaging material storage. The operation rooms or storage rooms of other posts cannot be used as passages for materials and operators to enter this post, and oven-like equipment cannot be used as passages for personnel. This can effectively prevent cross-contamination of different types of food caused by material transportation and operator flow.
5. Without affecting the process flow, process operations, and equipment layout, if the air-conditioning system parameters of adjacent clean operating rooms are the same, doors can be opened on the partition walls, pass boxes can be opened, or conveyor belts can be set up to transfer materials. Try to use less or no shared passageway outside the clean operation room.
6. If the crushing, sieving, tableting, filling, API drying and other positions that generate large amounts of dust cannot be fully enclosed, in addition to the necessary dust capture and dust removal devices, an operation front room should also be designed. To avoid contamination of adjacent rooms or shared walkways. In addition, for positions with a large amount of heat and moisture dissipation, such as solid preparation slurry preparation and injection concentration preparation, in addition to designing a moisture removal device, a front room can also be designed to avoid affecting the operation of the adjacent clean room due to large moisture dissipation and heat dissipation and ambient air conditioning parameters.
7. It is best to separate the elevators for transporting materials and elevators in multi-room factories. It can facilitate the layout of personnel flow and material flow. Because elevators and shafts are a large source of pollution, and the air in elevators and shafts is difficult to purify. Therefore, it is not suitable to install elevators in clean areas. If due to special requirements of the process or limitations of the factory building structure, the process equipment needs to be arranged three-dimensionally, and the materials need to be transported from top to bottom or bottom to top in clean area by elevator, an airlock should be installed between the elevator and the clean production area. Or design other measures to ensure air cleanliness in production area.
8. After people enter the workshop through the first change room and the second change room, and objects enter the workshop through the material flow passageway and the personnel flow passageway in GMP clean room are inseparable. All materials are processed by people. The operation is not so strict after coming in.
9. Personnel flow passageway should also be designed taking into account the total area and the use of goods. Some company staff changing rooms, buffer rooms, etc. are designed for only a few square meters, and the actual space for changing clothes is small.
10. It is necessary to effectively avoid the intersection of personnel flow, material flow, equipment flow, and waste flow. It is impossible to ensure perfect rationality in actual design process. There will be multiple types of collinear production workshops, and different working modes of equipment.
11. The same is true for logistics. There will be various risks. The changing procedures are not standardized, the materials access is not standardized, and some may have poorly designed escape routes. If disasters such as earthquakes and fires occur, when you are in a canning area or a nearby place where you need to change clothes several times, it is actually very dangerous because the space designed by GMP clean room is narrow and there is no special escape window or breakable part.
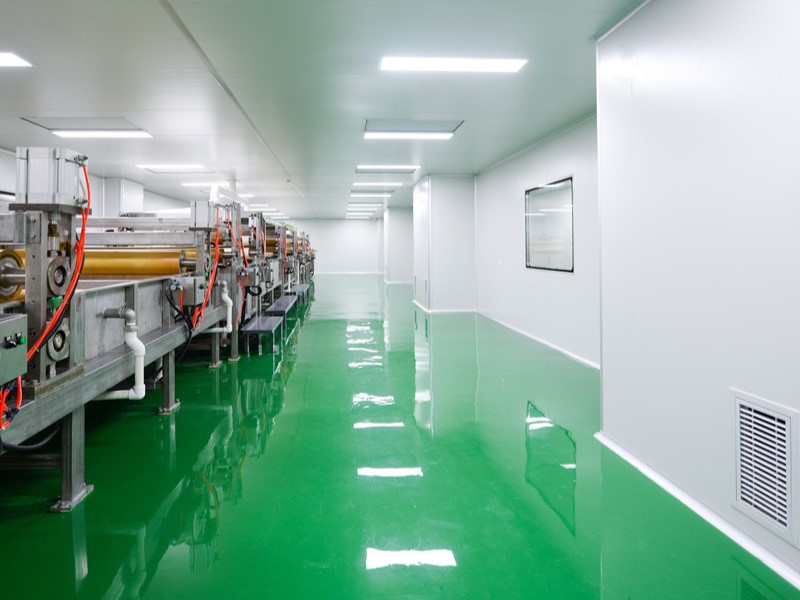
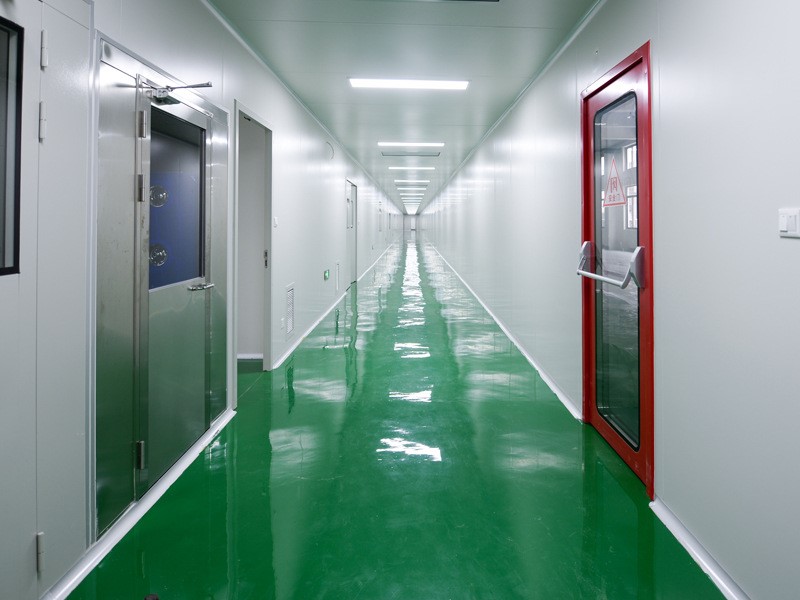
Post time: Sep-26-2023