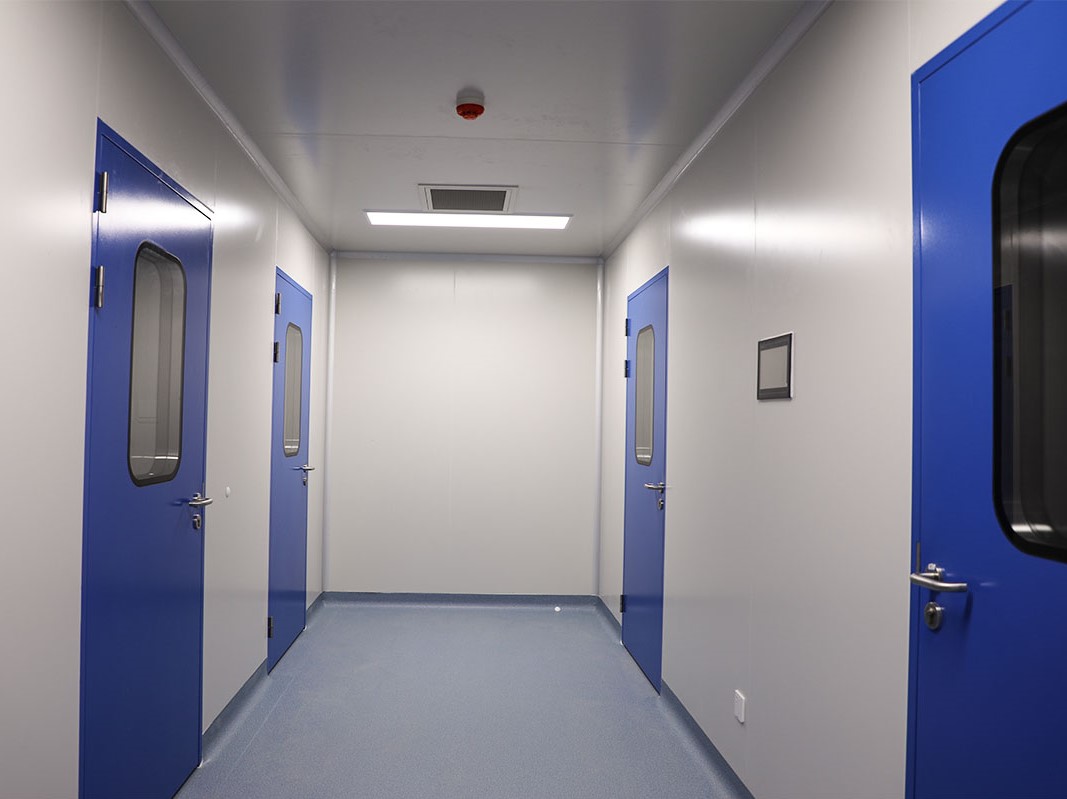
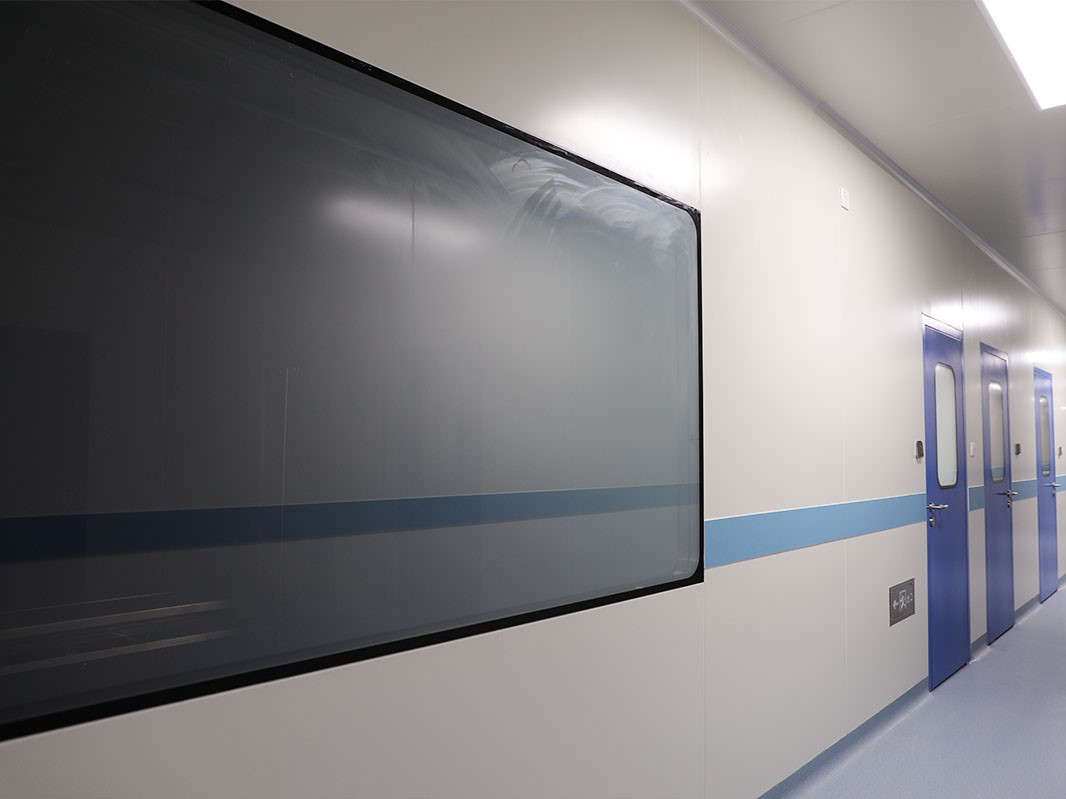
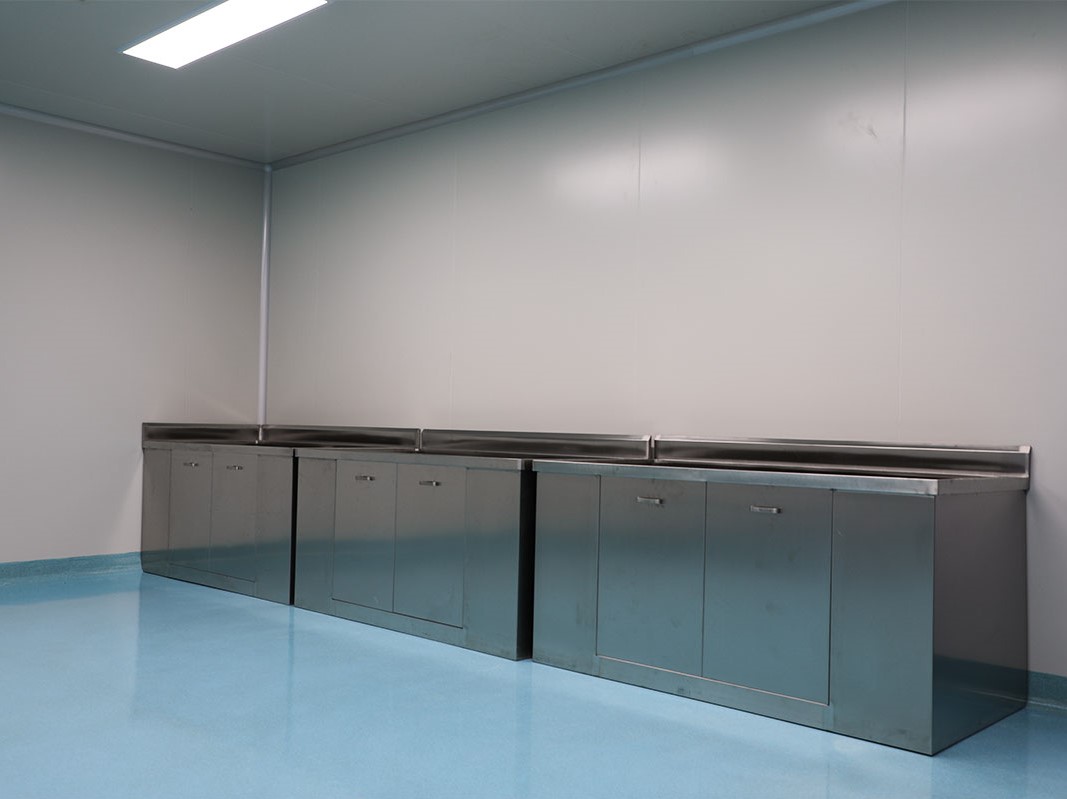
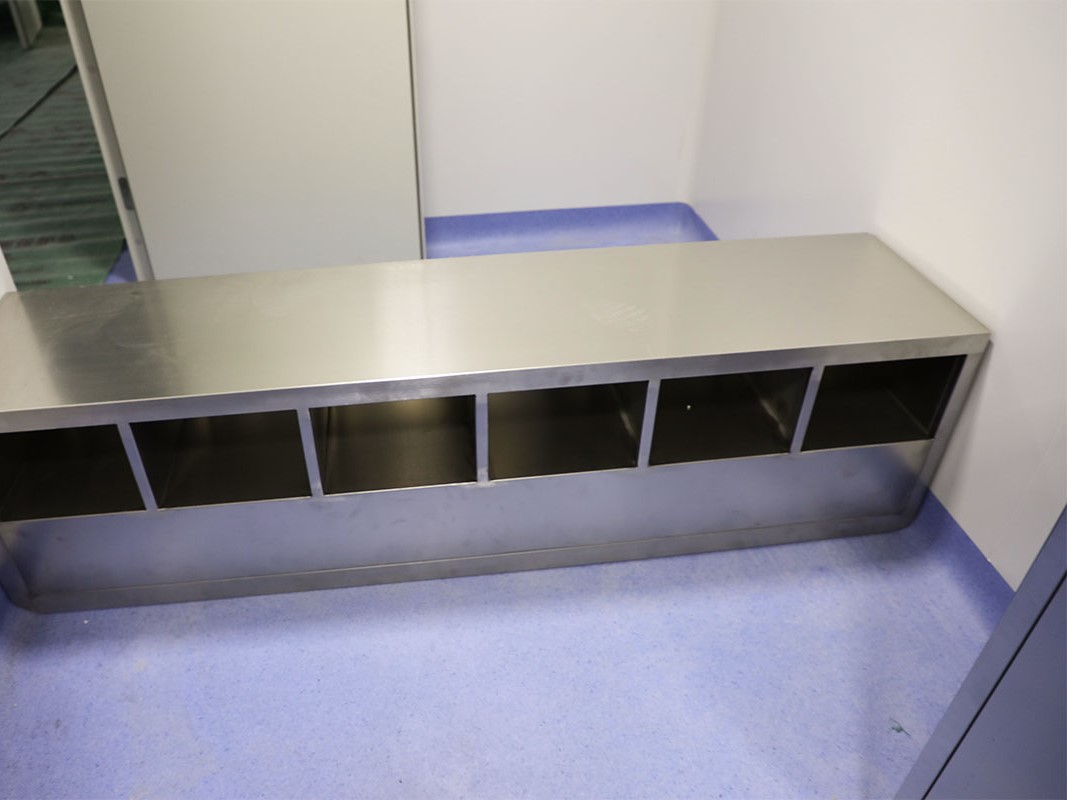
Since its promulgation in 1992, the "Good Manufacturing Practice for Drugs" (GMP) in China's pharmaceutical industry has gradually been recognized, accepted, and implemented by pharmaceutical production enterprises. GMP is a national mandatory policy for enterprises, and enterprises that fail to meet the requirements within the specified time limit will cease production.
The core content of GMP certification is the quality management control of drug production. Its content can be summarized into two parts: software management and hardware facilities. The clean room building is one of the major investment components in hardware facilities. After the completion of the clean room building, whether it can achieve the design objectives and meet GMP requirements must ultimately be confirmed through testing.
During the inspection of clean room, some of them failed the cleanliness inspection, some were local to the factory, and some were the entire project. If the inspection is not qualified, although both parties have achieved the requirements through rectification, debugging, cleaning, etc., it often wastes a lot of manpower and material resources, delays the construction period, and delays the process of GMP certification. Some reasons and defects can be avoided before testing. In our actual work, we have found that the main reasons and improvement measures for unqualified cleanliness and GMP failure include:
1. Unreasonable engineering design
This phenomenon is relatively rare, mainly in the construction of small clean rooms with low cleanliness requirements. The competition in clean room engineering is relatively fierce now, and some construction units have provided lower quotations in their bids to obtain the project. In the later stage of construction, some units were used to cut corners and use lower power air conditioning and ventilation compressor units due to their lack of knowledge, resulting in mismatched supply power and clean area, resulting in unqualified cleanliness. Another reason is that the user has added new requirements and clean area after the design and construction start, which will also make the original design unable to meet the requirements. This congenital defect is difficult to improve and should be avoided during the engineering design phase.
2. Replacing high-end products with low-end products
In the application of hepa filters in clean rooms, the country stipulates that for air purification treatment with a cleanliness level of 100000 or above, three-level filtration of primary, medium, and hepa filters should be used. During the validation process, it was found that a large clean room project used a sub hepa air filter to replace the hepa air filter at a cleanliness level of 10000, resulting in unqualified cleanliness. Finally, the high-efficiency filter was replaced to meet the requirements of GMP certification.
3. Poor sealing of the air supply duct or filter
This phenomenon is caused by rough construction, and during acceptance, it may appear that a certain room or part of the same system is not qualified. The improvement method is to use the leakage test method for the air supply duct, and the filter uses a particle counter to scan the cross-section, sealing glue, and installation frame of the filter, identify the leakage location, and carefully seal it.
4. Poor design and commissioning of return air ducts or air vents
In terms of design reasons, sometimes due to space limitations, the use of "top supply side return" or insufficient number of return air vents is not feasible. After eliminating design reasons, the debugging of return air vents is also an important construction link. If the debugging is not good, the resistance of the return air outlet is too high, and the return air volume is less than the supply air volume, it will also cause unqualified cleanliness. In addition, the height of the return air outlet from the ground during construction also affects cleanliness.
5. Insufficient self purification time for the clean room system during testing
According to the national standard, the test effort shall be started 30 minutes after the purification air conditioning system operates normally. If the running time is too short, it can also cause unqualified cleanliness. In this case, it is sufficient to extend the operating time of the air conditioning purification system appropriately.
6. The purification air conditioning system was not cleaned thoroughly
During the construction process, the entire purification air conditioning system, especially the supply and return air ducts, is not completed in one go, and construction personnel and the construction environment can cause pollution to the ventilation ducts and filters. If not cleaned thoroughly, it will directly affect the test results. The improvement measure is to clean while constructing, and after the previous section of pipeline installation is thoroughly cleaned, plastic film can be used to seal it to avoid pollution caused by environmental factors.
7. Clean workshop not thoroughly cleaned
Undoubtedly, a clean workshop must be thoroughly cleaned before testing can proceed. Require the final wiping personnel to wear clean work clothes for cleaning to eliminate contamination caused by the cleaning personnel's human body. Cleaning agents can be tap water, pure water, organic solvents, neutral detergents, etc. For those with anti-static requirements, wipe thoroughly with a cloth dipped in anti-static liquid.
Post time: Jul-26-2023