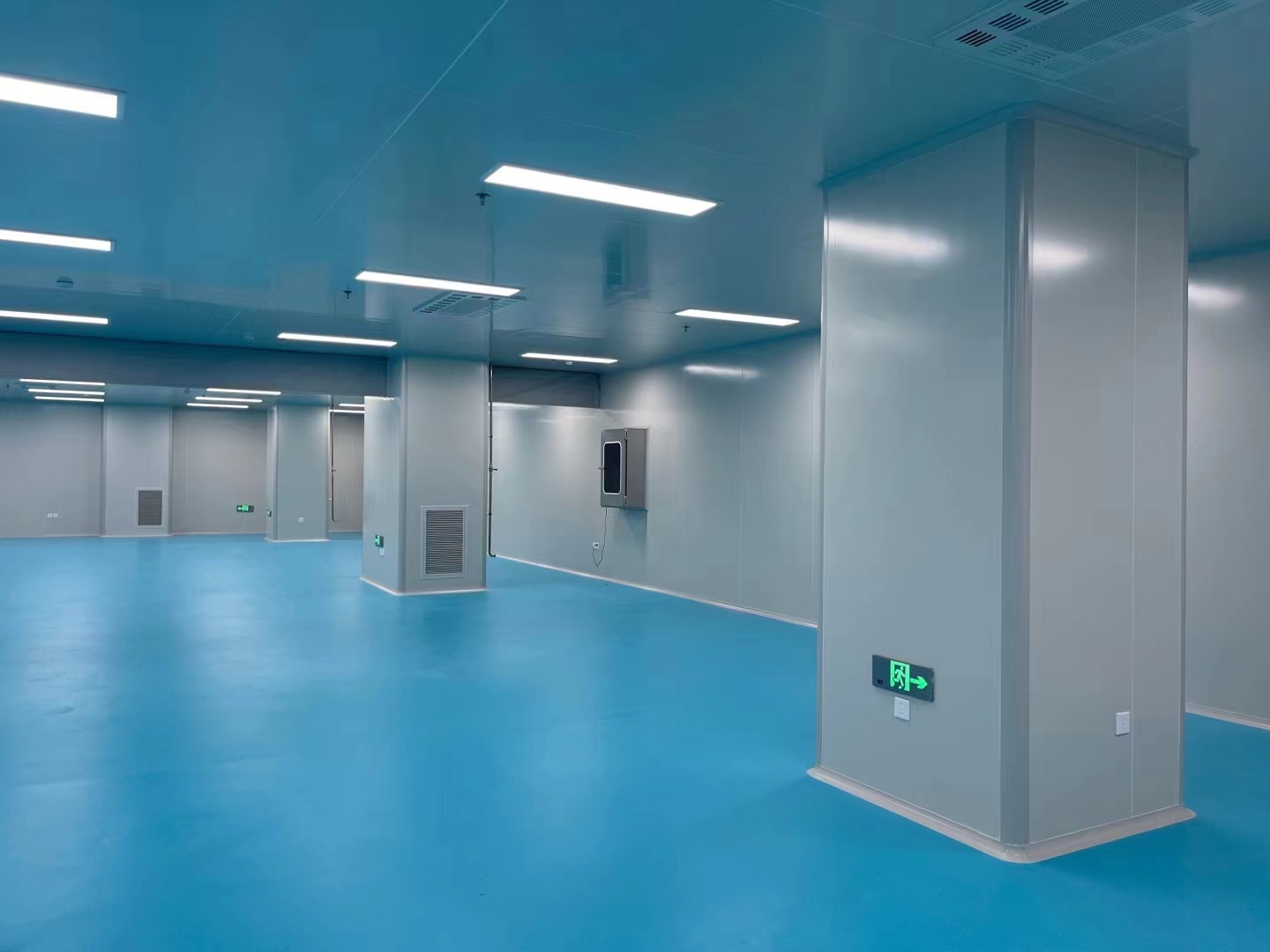
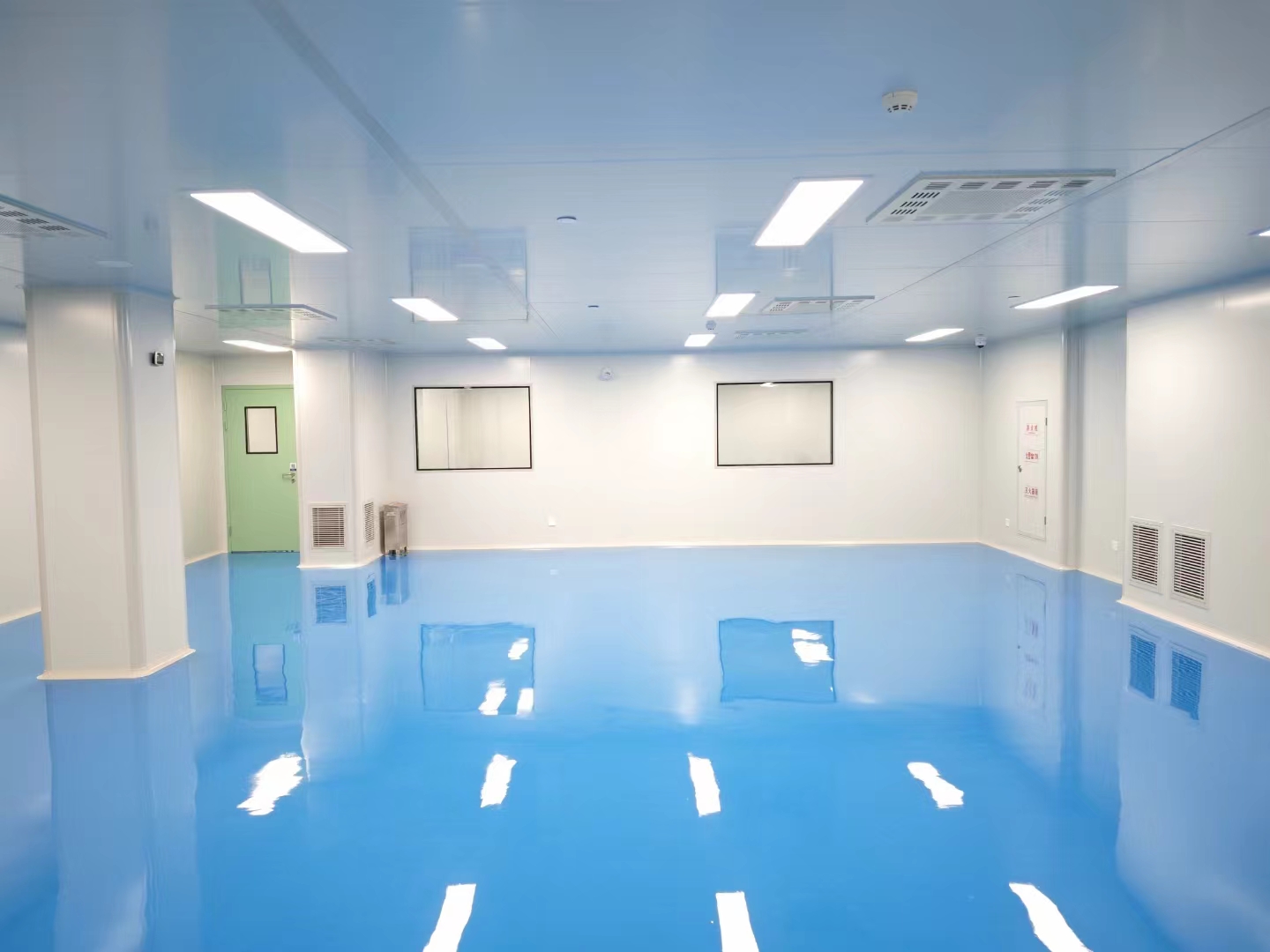
In order to better serve customers and design according to their needs, at the beginning of the design, some factors need to be considered and measured to achieve reasonable planning. The clean room design plan needs to follow the following steps:
1. Collect basic information required for design
Clean room plan, production scale, production methods and production processes, technical specifications of raw materials and intermediate products, finished product packaging forms and specifications, construction scale, land use and special requirements of the builder, etc for reconstruction projects, original materials should also be collected as design resources.
2. Preliminarily determine the workshop area and structural form
Based on the product variety, scale and construction scale, initially determine the functional rooms (production area, auxiliary area) that should be set up in clean room, and then determine the approximate building area, structural form or number of building floors of the workshop based on the overall planning of the factory.
3.Material balance
Make a material budget based on product output, production shifts and production characteristics. The clean room project calculates the amount of input materials (raw materials, auxiliary materials), packaging materials (bottles, stoppers, aluminum caps), and process water consumption for each batch of production.
4. Equipment selection
According to the batch production determined by the material scale, select the appropriate equipment and number of units, the suitability of single machine production and linkage line production, and the requirements of the construction unit.
5. Workshop capacity
Determine the number of workshop personnel based on output and equipment selection operation requirements.
Clean room design
After completing above work, the graphic design can be carried out. The design ideas at this stage are as follows;
①. Determine the location of the entrance and exit of the workshop’s personnel flow.
The people's logistics route must be reasonable and short, without interfering with each other, and consistent with the overall people's logistics route in the factory area.
②. Divide production lines and auxiliary areas
(Including clean room system refrigeration, power distribution, water production stations, etc.) The location within the workshop, such as warehouses, offices, quality inspection, etc., should be comprehensively considered in clean room. The design principles are reasonable pedestrian flow routes, no cross-interference with each other, easy operation, relatively independent areas, no interference with each other, and the shortest fluid transportation pipeline.
③. Design function room
Whether it is an auxiliary area or a production line, it should meet production requirements and operation convenience, minimize the transportation of materials and personnel, and functions must not pass through each other; clean areas and non-clean areas, aseptic operating areas and non-sterile areas The operating area can be effectively separated.
④. Reasonable adjustments
After completing preliminary layout, further analyze the rationality of the layout and make reasonable and appropriate adjustments to obtain the best layout.
Post time: Mar-25-2024